Brianna Karelin was a junior at the University of Cincinnati, majoring in construction management, when she flew across the country for a co-op at Helix Electric in San Francisco. Karelin had worked in construction since the age of 16, and her bosses had always been micromanagers. Now she was working on a seven-story assisted living facility, and her boss was a forward thinker, focused on improving efficiency in the construction industry and updating processes that had remained the same for the past 50 years. “My boss basically told me, ‘I want you to put everything we’ll need for the electrical rough-in stage of construction for each individual unit in a box. I want the things inside the box to be as put together as much as possible.’ Those were his instructions,” Karelin recalled. She realized that what he was asking for was a more efficient process, one that was repeatable and minimized errors. “Give me two weeks,” she told him, “I’ll give you something decent. Give me a month and I’ll come up with something great.”
A picture (in Revu) is worth a thousand words
And that’s exactly what she did. Using Bluebeam Revu, a software she’d had some experience with at Cincinnati, Karelin essentially used the tool set feature to create an easy system of drag and drop. She also used Revu to set up a template worksheet so it would take a minute or less to design an electrical box. This also allowed her to indicate to the installers in the field what that box should look like. Previously, all that information would have been spelled out, leaving lots of room for confusion and error. Now, the actual drawing could be given to the person in the prefab shop working on the floor, so they have an actual picture of what they’re supposed to build. Plus, Karelin color-coded everything, which further minimized the risk of error.
Her bosses were impressed, to say the least. Nearing the end of her co-op term, Helix extended a full-time offer with a newly created position based on her new process. Karelin even got to write her own job description.
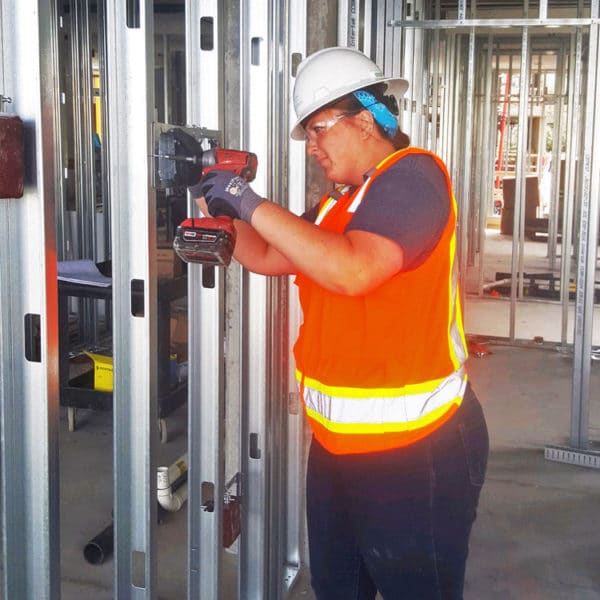
Prefabrication can help offset the labor shortage
Now Karelin works as a prefabrication engineer at Helix Electric’s Lake Elsinore prefabrication shop, improving current prefab processes for the shop and the field. Beginning next year, she’ll begin rolling these out onto jobsites from Honolulu to Seattle. She sees prefabrication as a key to overcoming the challenges of a tight labor market for the trades—a problem with no end in sight.
“Prefabrication is important because construction is doing really well right now, so we’re getting all these projects, but we don’t necessarily have all the people to stack them. If we can improve the productivity on a jobsite, that helps alleviate some of the stress on the crews as well as our other project teams, because we don’t have infinite resources at this point,” Karelin said. She has been increasingly turning to Revu to help support these changes and, in turn, reduce Helix’s overall tech stack. The more one software can do, the more that data gets shared efficiently, and the less companies need to spend on technology and training.
The bottom line is that with only so many people to work on projects, and with that number decreasing for the foreseeable future, contractors will have to turn to improvements in productivity through tech and innovation to stay on top. Brianna Karelin is looking out for that bottom line.