Before the lights come up and the bass hits your chest, there’s the build.
Not the band. Not the roadies. The real build—the one made of steel trusses, acoustic panels, cantilevered decks and 20,000 perfectly placed seats.
From Red Rocks to The Sphere, concert venues aren’t just places where people go to hear music. They are music—shaped by stone, concrete, wood and sound science. But none of it works without builders. Without crews who can pour a stage slab to within an eighth of an inch or jack a 200-ton acoustic ceiling into place without cracking the dome above.
Here’s how some of the most legendary music venues in the world were engineered to rock—and what those projects say about the precision, collaboration and craftsmanship behind the scenes.
Red Rocks Amphitheatre (Colorado, USA)
Red Rocks is one of the only concert venues on Earth shaped largely by geology. The amphitheater sits nestled between 300-foot monoliths—Ship Rock and Creation Rock—which naturally reflect and amplify sound across the bowl. The venue’s “outdoor cathedral” acoustics are the result of perfect topography, but its longevity comes from precision construction.
In 2021, the venue underwent a major structural upgrade: a new copper-clad tension-grid roof was installed above the stage, increasing rigging capacity from 36,000 to 150,000 pounds and offering new acoustic control through Douglas fir paneling beneath. Designers and crews had to match this addition to the character—and natural echo chamber—of the historic rock bowl without compromising acoustics or visuals.
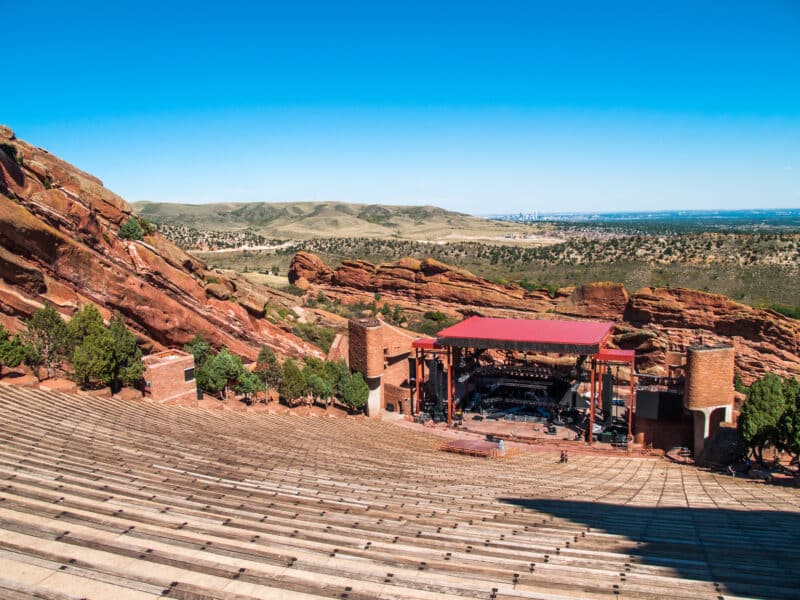
The O2 Arena (London, UK)
Ever built a full concert venue inside a giant fabric dome? That’s exactly what happened with The O2 Arena, formerly the Millennium Dome. The construction team prefabricated the acoustic roof on the ground—layering perforated aluminum, mineral wool and steel for extreme bass containment—then hydraulically jacked it into place under the tented roof.
Engineers had to leave a precise 4-meter ventilation gap between the steel structure and the fabric above while maintaining tight tolerances for sound isolation and fire safety. The result is a venue with massive scale and surprisingly intimate, controlled sound.
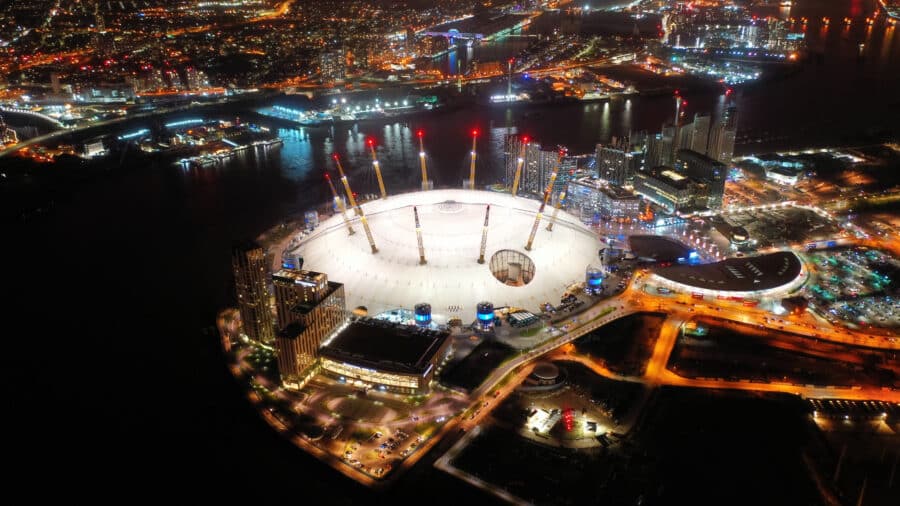
The Ryman Auditorium (Nashville, USA)
Originally built as a tabernacle in 1892, the Ryman Auditorium has acoustics so natural and resonant that artists barely need amplification. Its signature sound comes from its horseshoe-shaped balcony, hard plaster walls and 100-year-old curved pews—all of which diffuse sound organically.
When the venue was renovated in the 1990s and again in 2015, crews were instructed not to tamper with the sound. Updates to lighting, HVAC and even seating upholstery were made using materials carefully selected to preserve the venue’s warm reverb and natural brightness.

The Sphere (Las Vegas, USA)
The newest member of the “engineered to rock” club is also the most high-tech. The Sphere in Las Vegas is an immersive audio-visual arena with 18,600 seats, a 16K LED interior surface and more than 167,000 beamforming speakers embedded in the walls. Every seat gets a spatially targeted audio mix.
Construction-wise, The Sphere pushed every boundary. Crews installed a vibration-isolated, haptic-enabled floor to transmit bass through your body. Overhead, a domed steel grid supports the world’s largest curved display. Every surface had to be installed with millimeter precision to avoid latency, echo or comb filtering.
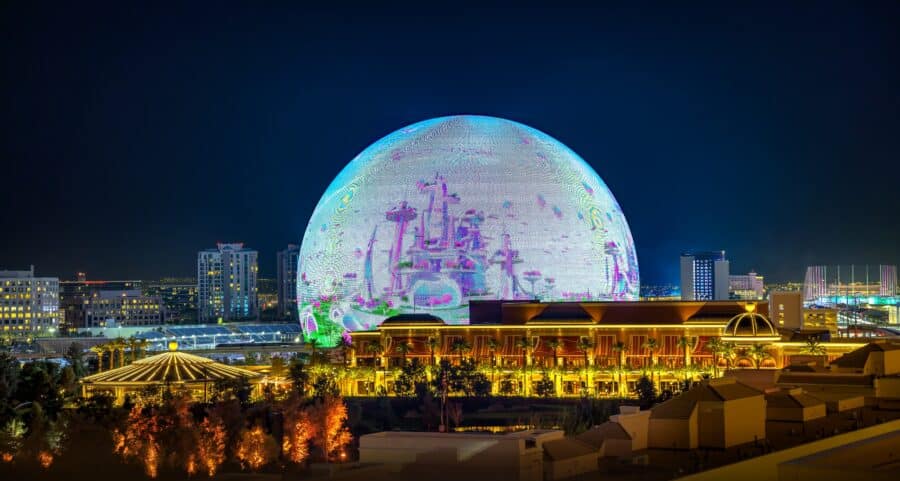
The Physics of Good Sound
Great sound isn’t just about speakers. It’s about what you build around them. Here’s how acoustics really work, and what construction has to do with it.
Reverb vs. Echo:
- Reverb = smooth tail of sound.
- Echo = delayed bounce-back that muddies everything.
What controls it? Surfaces, shapes and how precisely they’re installed.
Absorption Matters:
Different materials absorb sound differently:
- Concrete reflects.
- Mineral wool and fabric absorb.
- Wood and acoustic panels do both—if placed right.
Room Shape = Sound Shape:
Parallel walls trap “standing waves.” Curves, tiers and angles diffuse sound evenly. Bad geometry = dead spots and hotspots.
Standing Waves:
These happen when sound reflects perfectly and either cancels out or stacks. One row thumps. The next? Nothing.
Fix: bass traps, angled walls and proper AV tuning after install.
……
Global Sound Legends
Sydney Opera House (Australia)
A marvel of form and function, the Sydney Opera House suffered from poor sound in its Concert Hall for decades—until a 2022 retrofit added 18 massive “petal” reflectors over the stage. These curved fiberglass panels can be raised or lowered to optimize acoustics for different performances. Construction teams had to integrate them into Utzon’s heritage architecture without altering the hall’s iconic look.
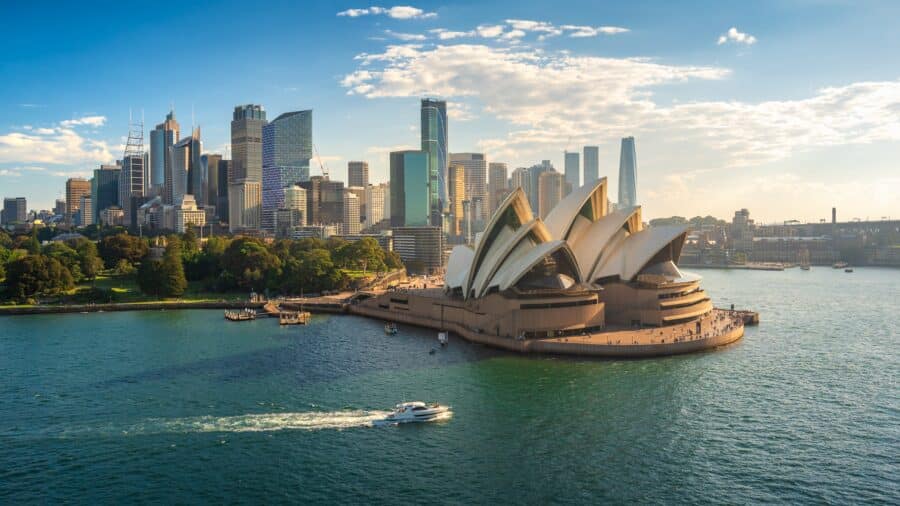
Walt Disney Concert Hall (Los Angeles, USA)
Designed by Frank Gehry and tuned by Yasuhisa Toyota, Disney Hall features vineyard-style seating, floating acoustic “sails” and a warm Douglas fir interior. During design, the team tested a 1:10 scale model filled with nitrogen to simulate real sound conditions. Even the HVAC ducts were shaped with airflow velocity and sound clarity in mind.
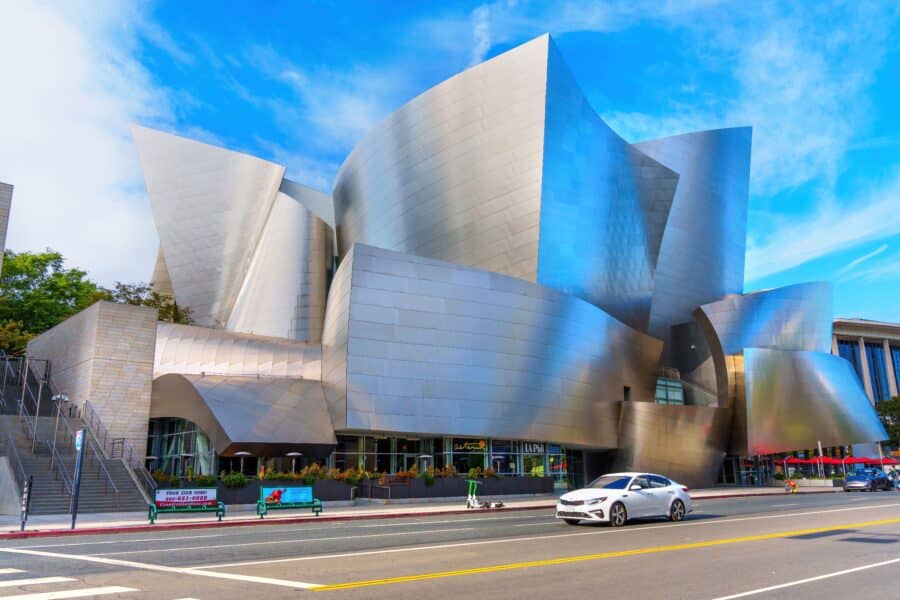
Berlin Philharmonie (Germany)
Home to the Berlin Philharmonic, this 1963 venue pioneered the now-standard “vineyard” seating layout. Scharoun’s design placed the orchestra in the center of tiered terraces, surrounded by convex reflector clouds and sound-absorbing materials. The result: crisp diffusion and perfect sightlines in every direction.
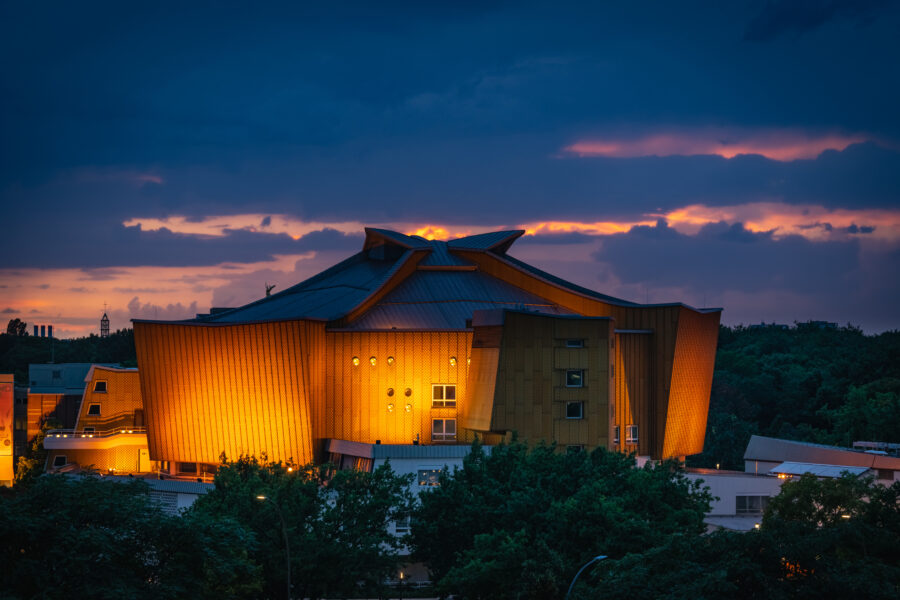
What Construction Pros Can Learn
Behind every legendary performance is a construction team that made it possible. Acoustic design is just the blueprint. Execution is what makes the room sing.
- Precision is non-negotiable. One misaligned acoustic panel can wreck clarity.
- Materials matter. Concrete, wood, mesh and upholstery all affect reverberation and absorption rates.
- Coordination is everything. Architects, MEP engineers, AV specialists and structural crews must be in constant sync.
- Mockups and field-testing work. From scale models (like Disney Hall) to full sound checks (like The Sphere), testing saves rework.
Built to Be Heard
The best concert venues don’t just host music. They become part of the music.
If you’re in the business of building spaces—concert halls or skyscrapers or residential homes—you know it’s not about showing off. It’s about getting it right.
Because when you do, people don’t just hear the difference. They feel it.