A brief history of timber construction
For centuries, buildings were made mostly of wood. With trees plentiful and building material technology in its infancy, timber buildings held sway.
With the advent of brick, then steel and concrete, timber took a back seat in construction. Steel and concrete buildings could go higher, be stronger and last longer.
But sourcing and using these materials takes a toll on the environment. With concerns mounting over climate change in recent years—and construction’s contribution to it—timber has made a comeback.
What is mass timber?
Mass timber comprises sections of wood that have been engineered into structural panels, posts or beams, which are then glued under pressure or nailed together in layers. These layers are stacked in a perpendicular pattern for added strength.
According to the Forest Stewardship Council (FSC), mass timber, while lighter, can be superior to concrete and steel alternatives.
Types of mass timber
Cross-laminated timber (CLT)
The origins of the best known form of mass timber, cross-laminated timber (CLT), are in the forested regions of central Europe and Scandinavia, but it began making its mark in the modern construction industry around 30 years ago in Switzerland and Austria.
CLT consists of layers of kiln-dried dimension wood, which, says Naturally: Wood, a branch of Forestry Innovation Investment, is oriented at right angles to one another and then glued to form structural panels. “By gluing layers of wood at right angles, the panel delivers excellent structural rigidity in both directions,” it adds.
According to the FSC, CLT is “particularly well-suited for large floors, walls and ceilings, and it can withstand heavy traffic and multi-purpose buildings.” The FSC says CLT’s lightweight properties also offer “flexibility and superior resilience against wind loads.”
The BRE, a UK-based group of built environment researchers, scientists, engineers and technicians, points to CLT’s ability to provide “dry, fast onsite construction, with good potential for airtightness and a robust wall and floor structure suitable for most finishes internally and externally.”
The BRE notes that CLT requires only limited new skills to work with, while its low weight means a high degree of offsite manufacture is possible, making site work potentially cleaner and more efficient.
Nail-laminated timber (NLT)
There are other types of mass timber beyond CLT. Nail-laminated timber (NLT), which dates back more than 100 years, comprises sections of wood that have been nailed together.
The “Think Wood” campaign says NLT’s revival is due in large part to domestic availability. It doesn’t require a dedicated manufacturing facility, unlike CLT, and can be fabricated with readily available timber.
Dowel-laminated timber features sections of wood that are connected using dowel rods, rather than being glued, to form semi-fabricated floor and roof panels, says fabricator Eurban.
Glued laminated timber (Glulam)
It’s not all nail and dowel rods, however. Glue has its place in the pantheon of mass timber beyond CLT. Glulam is made by securing together laminates of timber that have already been planned to a smooth surface using glue.
Benefits of mass timber construction
The benefits of mass timber construction are numerous. As US construction firm CD Construction (CDC) points out, wood is a natural, renewable and sustainable material for building, with a lighter carbon footprint than steel or concrete.
It has also proven to be structurally strong and meet the same performance and life safety standards as concrete and steel structures.
And as wood sequesters carbon, timber buildings tackle the issue of emissions. CDC says an 18-storey mass timber building, for example, has a negative carbon imprint equal to taking 2,350 cars off the road per year.
In the light of recent tragic fires affecting buildings made with concrete and steel, concerns around the use of timber in residential developments, particularly high rise, are understandable.
Yet according to green building consultants GreenSpec, CLT panels can be produced to resist fire—via the process of “charring,” where the outer layer of wood burns but effectively insulates the inner core from the fire—anywhere from 30 to 90 minutes. “Fire performance in a [CLT] fire is a long way from their timber frame cousins,” it adds.
Concerns remain, however, and industry observers say it is imperative that developers work with fire safety experts from an early stage in a project and consider full-scale testing and modelling for fire.
Drawbacks of mass timber construction
When it comes to the downsides of mass timber construction, the Building Materials Safety Coalition in the US highlights a number of issues, including supply chain and schedule risks from limited CLT availability; a lack of experienced labour to install the material; and the impact of CLT—especially exposed beams—on insurance rates and project liabilities.
According to financial services specialist firm Gallagher, knowledge within the insurance sector around timber—both at broker and insurer level—is relatively scant.
“There is also a lack of hard, statistical experience, meaning insurers have to base their pricing on a limited sample size, and a sample size which unfortunately in the UK does contain some large fire losses,” Gallagher said.
All this makes placing timber risks into what is already a hard market much more challenging, the group adds.
Andrew Carpenter, chief executive of the Structural Timber Association, said increasing the use of structural timber is therefore vital in the quest to meet construction’s net zero obligations. “But the industry should adopt a pragmatic approach towards hybrid construction in order to overcome insurance hurdles.”
He adds: “The insurance industry must also be confident that the performance of the material is matched by the competency of those installing it.”
Examples of mass timber buildings
One of the most famous instances of a tall modern wooden building is Mjøstårnet in Norway. Completed in 2019, the 18-storey mixed-use tower stands 85 metres high and was erected in sections that were assembled on the ground before being craned into position.
In London, Dalston Works laid claim to being the world’s largest CLT building when it was finished in 2017. At 10 storeys tall, the 121-unit residential development is made entirely of CLT, from the external, party and core walls, floors and stairs.
Dalston Works weighs a fifth as much as a similarly sized concrete building, and the number of deliveries during construction was reduced by 80%, according to architect Waugh Thistleton.
And in Sweden, the Sara Cultural Centre in Skellefteå is a 75-metre tall, 20-storey hotel constructed of premanufactured modules in CLT stacked between two elevator cores. “Thanks to the placement and design of the cores, they can be entirely made from CLT,” says architect White Arkitekter.
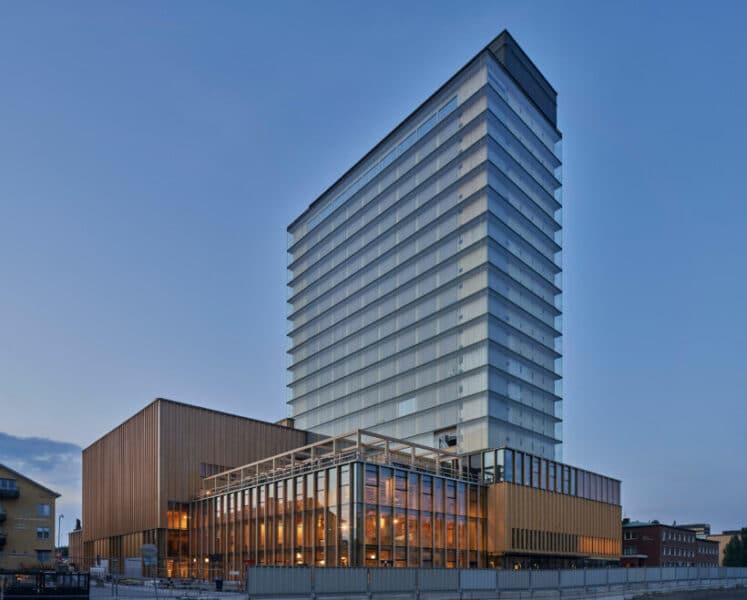
Are mass timber buildings the future?
In these climate-conscious times, the use of mass timber will prove attractive. There are indeed risks, and the issue of mass timber’s ability to resist fire will feature prominently on any list of occupiers’ FAQs, along with those of building inspectors worldwide.
That said, with sustainability and environmental considerations increasing, mass timber products like CLT look set to increase market share and play a bigger role in helping to deliver a greener built environment.