Construction is one of America’s largest and most complex industries. That complexity is why there is so much waste in materials and man-hours, and it is exactly why the lean approach is taking hold with AEC professionals.
There is a growing community of lean builders meeting online and in-person to share techniques and progress with one another to improve their work, relationships and to refine their practices.
But what is the lean approach? The lean approach was formalized in 1992 with these five principles:
- Define Value: Determine and define what your customers value. What do they want?
- Map Value Stream: What gets the most value to your customers? What is waste?
- Create Flow: After removing waste, simplify and formalize the steps to creating value.
- Establish Pull: By removing wasted efforts and excess, you’re more responsive in the moment to customer’s needs, which increases value delivered.
- Pursue Perfection: The most important step is continuing to refine steps 1-4, as well as to build a lean culture within your team.
Today, the Lean Construction Institute (LCI) is the tip of the spear for lean practices in the AEC industries. Founded in 1997, there are currently 26 LCI communities across the country. Membership includes companies such as the Fluor Corp., Jacobs, Turner Construction Co., Skanska Construction and many more of the largest AEC companies in the country.
We caught up with member representatives of the LCI to talk about their experience with the lean approach as well as learn about the challenges they’ve encountered and the value they’ve received from embracing lean techniques.
Cut waste with transparency
Peter Ukstins, a construction risk engineering consultant at AXA XL, said that transparency is vital to reducing risk and waste. “We see a lot of rework … a lot of unreliable commitments being made on projects, and that all effects the bottom line,” Ukstins said.
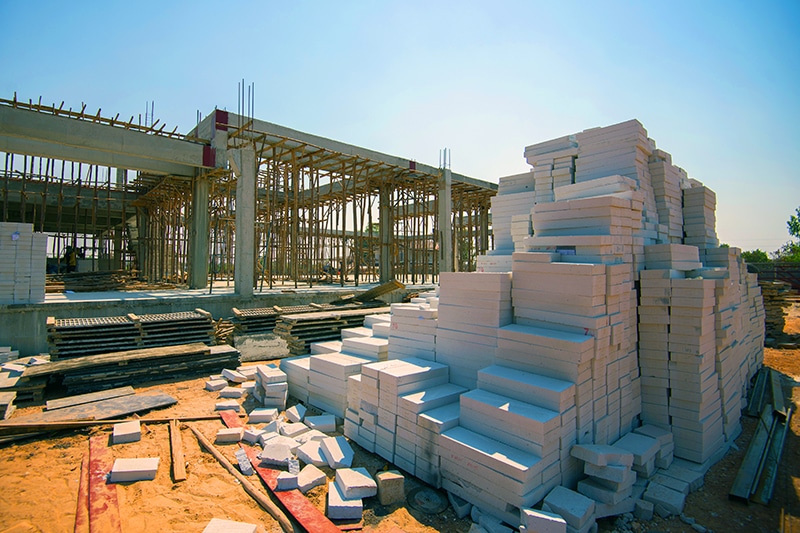
Rework, or any extra or redundant effort, is waste, and eliminating waste is one of the pillars of any lean approach. Once you have identified what your clients value, you can work backwards to identify waste, which is anything that doesn’t directly contribute to creating that value, and take steps to minimize or eliminate the waste.
Unreliable commitments are a common pain point in construction because of the variety of stakeholders and contractors needed for large projects. A delay from one subcontractor can create costly delays for everyone, which is a risk that has to be mitigated early on to minimize such waste.
Amanda Patton, manager of integrated projects at Balfour Beatty, suggested AEC professionals should look at “how can we bring everybody’s expertise to the table, how can we put risk management in the hands of the people who are closest to the work and have the most knowledge about it.” Reliable, honest commitments about what a job takes result in higher customer and team satisfaction, according to Patton, as well as reduce waste.
Pursuing such transparency among stakeholders accustomed to guarding their own silos can be difficult, however, and often requires training and on-boarding.
Erin Miller, a mechanical engineer for Southland, said that one of the first steps to implementing lean is creating a lean culture in your own office. Miller said that “We [Southland] start with our people … really empowering your frontline, your doers, your people in the field, getting them to speak up and improve the process that they’re working with, because they’re most closely aligned with the work.”
Setting standards for what already works
Kurt Maldovan, a director of digital delivery at Jacobs, emphasized that many builders use lean techniques with a story about “taking the last planner, using Post-its to schedule backwards and pull forward the activities that add the most value” to construction managers.
Moldovan found that “superintendents would say, ‘Well, that’s what I do today. It just wasn’t completely apparent.’” He adds that what makes lean useful and practical is “bringing to light what folks do on a day-to-day basis but formalizing it to a degree.”
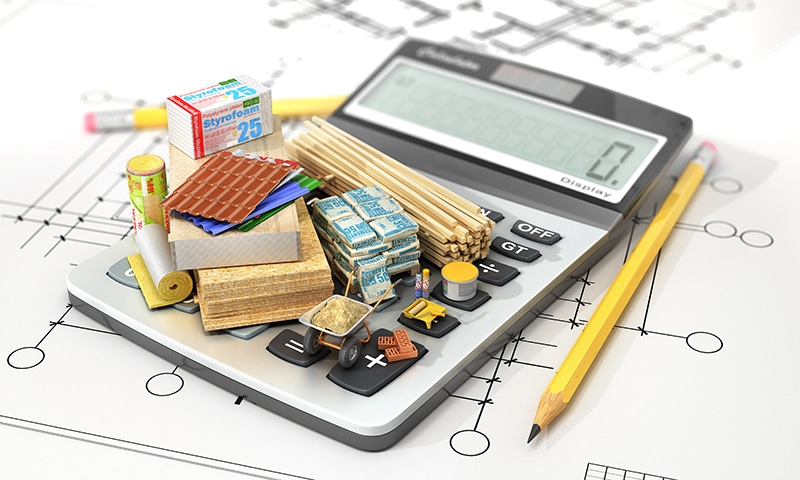
Miller agreed, describing how she had to overcome the assumptions of foremen and superintendents that lean was a way to change what they’re doing. Instead, it’s a way to “pull that knowledge and … start sharing it with the younger generations, putting that information into designs and planning.”
Patton said that by explaining that information isn’t always shared because people don’t ask if it’s valuable to the “next person on the line.” Waste can be cut, she said, often by simply asking, “How can we expand the conversation to include more people [and] to ask our customer: ‘Do you really need this information?’ Because a lot of us spend time producing things that people don’t really need if we ask them the question.”
Establishing goals
There are many ways to cut waste, but all of them start with honest and pragmatic conversations about what waste is. There are different types of waste—in materials, movement, processing and time. All kinds of waste can be cut by taking some extra time to plan and communicate before breaking ground.
Bluebeam Studio Sessions is an ideal platform for such collaboration. Patton described how her team uses “Studio Sessions to create public documents … we come together once a week as an entire team to give an update from the design and construction aspects.” It’s only a short meeting, Patton said, but it’s a chance for “everybody who owns information to put that information in to a document that’s shared with everybody.” This way, everyone knows what everyone is doing and can spot opportunities to cut redundant efforts and make efficient plans.
Communication is at the center of lean. That means transparency and respect, as everyone has to understand and share their goals. Patton described how, in her current project building the Pavilion for Penn Medicine, they put patient “personas” throughout the site “to remind the folks in the field that these are the people that we’re building this hospital for; this is the reason that we’re doing this. It’s not just about the nuts and bolts, literally; it’s more than that and you’re part of something bigger.”
Labor efficiency has increased across virtually all industries in the United States, even doubling in some cases. Only construction productivity has decreased. The usual suspects are behind this decline—a workforce that’s struggling to replace its aging workers; the competitive bid process for contractors and subcontractors; problems in cooperation between unions and trade contractors; and the risk-averse nature of most builders toward new technology or approaches.
Moldovan said that the answer to these problems can be answered by fostering a culture of respect for everyone’s specialties and silos, so the best ideas for cutting waste or adding value to a project can get into a plan early on, when it will add the most value. Lean techniques “go into planning, into design, close out, warranty … into technology and into personal lives,” Moldovan said. “Really, the foundation is respect for people.”