Franklin D. Roosevelt pronounced himself “awestruck” when, as governor of New York, he cut the ribbon in 1931 for the 102-story Empire State Building.
The Empire State Building is no longer the world’s tallest building—that honor now belongs to Burj Khalifa, in Dubai—although it managed to hang onto that title for decades until the early 1970s.
More than 90 years later, however, the iconic tower—in particular the story of its construction—continues to inspire awe among construction industry professionals.
In an age when it can take two to three years to build new towers half or even just a quarter of the size of the Empire State, the story of how the 1,250-foot skyscraper rose into the Manhattan skyline in a little more than 15 months still has engineers and construction experts shaking their heads in wonder.
Add in architectural and engineering work, and the whole project took Starrett Brothers and Eken, the legendary contractor, just 20 months to design and build.
Along the way, Paul and William Starrett developed techniques that were ahead of their time, foreshadowing construction industry practices that would develop over the coming decades.
“They were production managers for everything from the money and the materials to the labor,” said Sean Graystone, an industry consultant who specializes in lean construction techniques and historic building preservation.
“Certainly no one could put that building up in downtown New York today in that time,” Graystone said.
A blindingly fast start
The speed with which the Empire State Building was designed and built has yet to be surpassed and is breathtaking in comparison with other landmark skyscrapers.
It took three years (36 months) from groundbreaking to completion to build the old Sears Tower (now Willis Tower) in Chicago, which became the tallest building in the world when it opened in 1973. That’s not counting design and engineering work, which began a year before the project’s 1970 groundbreaking.
How could a tower of the size of the Empire State still hold the record for speed of construction—all while using the more labor-intensive and less technologically sophisticated building techniques of the early 1930s?
Founded by Paul Starrett, his brother William and fellow tower builder Arthur J. Eken, Starrett Brothers and Eken was the premier skyrise contractor of the day, having previously erected a number of prominent Manhattan buildings.
Before the Starretts went into business together in the 1920s, William had served as the master builder for the U.S. Army in World War I, while Paul had risen to lead one of the largest construction firms of the time.
The brothers had earned a reputation as geniuses of large-scale organization and planning—a brilliance that was on full display in the construction of the Empire State Building.
The project’s financiers, led by former New York Gov. Al Smith, were determined to win a race against the Chrysler Building, also under construction, to become the tallest tower in the world. This meant both going higher and opening first.
Drawing on their reputation as the world’s premier “skyline builders,” Starrett Brothers responded to the challenge by acting with a speed almost unimaginable today, starting with planning and design.
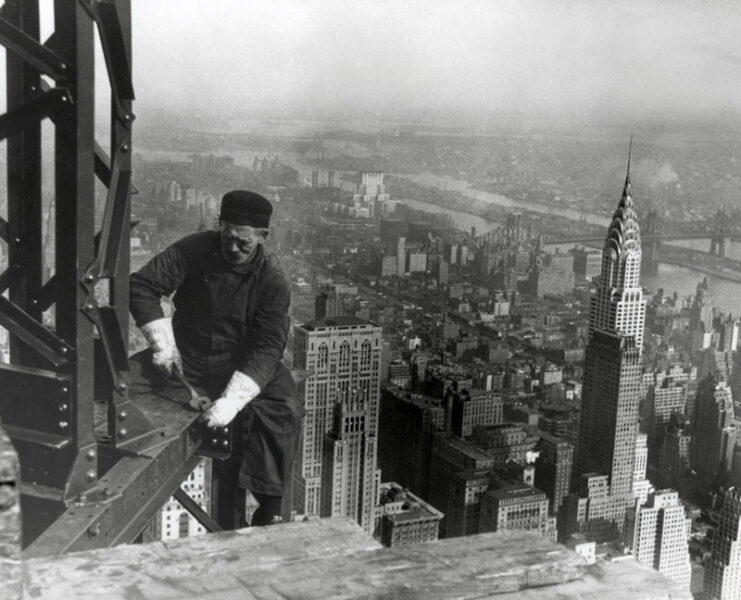
Architect William Lamb sketched out the design for the tower in two weeks, drawing upon earlier designs for a high-rise in Winston-Salem, N.C., according to Great Moments in Construction History.
The Starretts didn’t wait for all the design work to be finalized, however, before breaking ground, with the contractors using what would be called “fast-track” construction methods nowadays.
Starrett Brothers actually began foundation work before demolition was complete on the original Waldorf-Astoria Hotel, which occupied part of the site, a technique the Starretts had pioneered just a year earlier on a previous tower, 40 Wall Street, according to Construction Company.com.
As many as 600 workers, split into two shifts, worked 24 hours a day to dig out the foundation.
“This may be the first skyscraper that was fast-tracked,” said Donald Friedman, a structural engineer and co-author of “Building the Empire State,” among other books on construction and engineering. “Major design decisions were not complete when construction began. This is a huge amount of fast-tracking before I would have expected to see it.”
A focus on efficiency
As work moved from digging out the foundation to raising the tower itself, the ingenious Starretts effectively created a massive assembly line in the sky, using a just-in-time logistics system decades before the concept became fashionable.
Steel beams rolled out of the foundry in Pennsylvania, and in roughly 80 hours, they were hoisted into place on the tower’s steadily rising frame on a series of four derricks, Graystone said.
Each beam came pre-marked, with notations detailing what derrick, what side of the building and what floor it was to be raised into place, Graystone noted.
ALSO ON BUILT:
The Starretts’ keen understanding of the tower construction process enabled them to design around various choke points and ensure a steady flow of construction materials as they were needed.
To keep work at the site flowing smoothly, other materials were made at plants off-site in as near a finished state as possible before being delivered.
Starrett Brothers came up with ways of boosting the efficiency of their construction team as well, with 3,500 workers, divided into 60 different trades, toiling on the tower.
The Starretts rolled out a mini railway system, complete with tracks, on floors under construction, enabling workers to move much larger amounts of building materials around than they would have otherwise been able to do with wheelbarrows.
The contractors also established a series of cafeterias on the floors of the tower as it took shape, ensuring workers stayed on site during lunch hour and breaks.
“All the workers would have had to go out to the street for lunch,” Friedman said. “They reduced the demand on the stairs and elevators.”
“It was a remarkably smooth-running site, particularly given the size of the project and no staging area,” he added.
Achievements live on
All the Starretts’ efficiency, prescient planning and organizational genius couldn’t save the Empire State Building from the ravages of the Great Depression.
The tower opened on May 1, 1931, during the darkest days of the economic cataclysm. And while the tower quickly became a major tourist attraction and cultural icon, as a business proposition, it was a failure, quickly earning the nickname “The Empty State Building.”
The tower would not turn a profit until 1950, nearly two decades after it opened, although it eventually became a desirable location for corporate tenants.
But the brilliance of the Starrett Brothers’ achievement lives on, with the publication in 1998 by Carol Willis and Friedman of “Building the Empire State,” helping give the Starretts their rightful due.
The book came about after the discovery of an in-house notebook compiled by Starrett Brothers on the construction of the Empire State as it was happening. The construction diary was found in the files of the successor company to Starrett, HRH Construction Co.
The notebook included a treasure trove of details on the construction and architecture of the tower, such as a drawing laying out exactly what crane was to lift which piece of steel.
“It’s tough as a practicing engineer to get a handle on past practices,” Friedman said. “You see the result, but you don’t really know how it was done. It is interesting to see the ancestors of a lot of current practices.”