Washington, D.C., is home to some of the most historic buildings in the world, with design and structural influences tracing back to ancient Egypt and medieval Europe.
About 10 miles west of the nation’s capital is a facility whose primary aim is to push the architectural influences of its metropolitan neighbor deeper into the history books.
HITT Contracting Inc.’s Co|Lab, in Falls Church, Virginia, is an 8,600-square-foot, state-of-the-art building for design and construction professionals to experiment and prove new industry approaches.
Nestled in a neighborhood with mostly brick industrial buildings and a smattering of archetypal beltway-style townhomes, Co|Lab instantly pops through with its forward-looking architecture and modern aesthetic.
Co|Lab, which took about a year to build and opened in June 2019, isn’t just one of the country’s first true R&D facilities. It’s also built using innovative and sustainable materials and design concepts that make the building a functioning symbol of construction’s potential future.
“Co|Lab is a really exciting space for us,” said David Stone, HITT’s director of virtual construction. “It represents an opportunity for the construction and design industries to work together with our clients and to figure out a way to improve the way we deliver projects.”
A truly sustainable structure
Walking through Co|Lab is a unique experience.
The two-story building designed by architecture firm William McDonough + Partners is configured using a mass timber structure that uses cross-laminated timber (CLT) and glulam; a high-performance concrete rainscreen façade; and a roof-mounted solar panel array, according to HITT’s website.
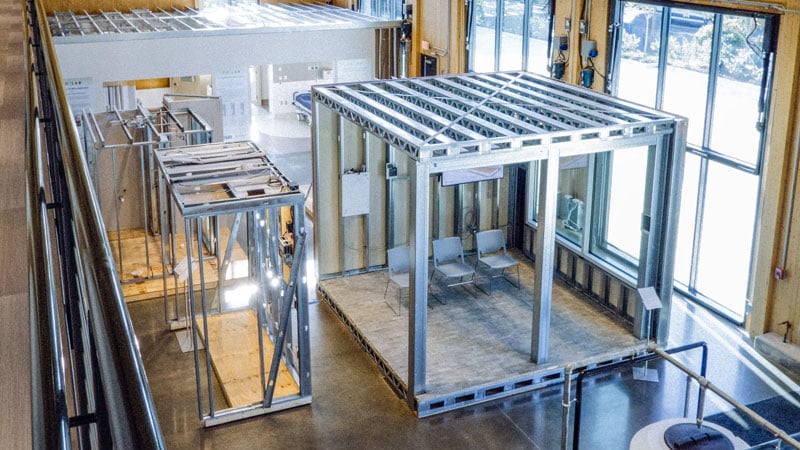
Co|Lab’s design also includes variable refrigerant flow HVAC systems, water-based Radiant Heat Flooring that uses electrical energy from the solar array to provide the facility with cost-effective heat year-round in the double-height bay space. HITT achieved a LEED v4 BD+C Platinum certification with the building—the first in the greater Washington, D.C., metro area to do so.
But wait … there’s more.
Co|Lab uses a BAS Controls + Dashboard, a component that allows it to track efficient building operations. “To achieve net zero operations,” the general contractor’s website says, “the rooftop solar array is projected to produce 118% of the building’s anticipated annual energy needs.”
Finally, Co|Lab is designed for disassembly—like a set of blocks.
“There are minimal adhesives in the building,” said Aidan Hitt, Co|Lab’s manager. “The carpets are even floating carpets, and the ceiling tiles are all individual pieces that can be disassembled quite easily.”
Creating construction’s future
Why did 85-year-old HITT build Co|Lab?
A big reason was to create an experimental space for it to test concepts before they’re implemented in the field on a job site. This is a rarity in an industry where most new approaches to design and build concepts are left to testing on live projects—a risky proposition, considering real dollars and expectations are on the line.
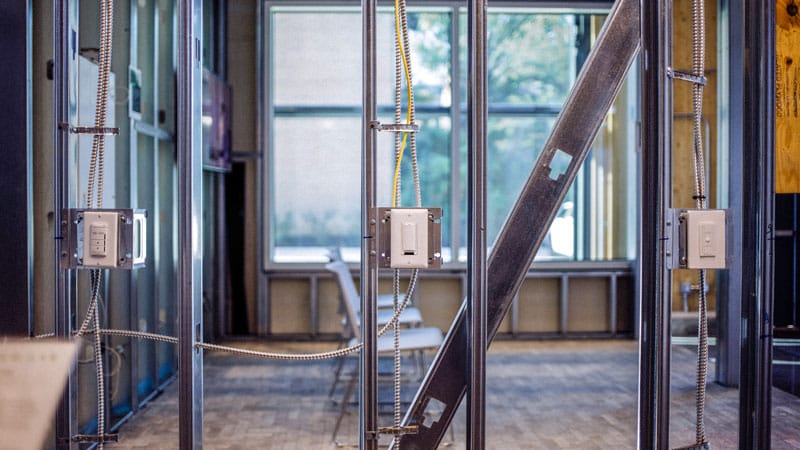
“We’ve always had research and development and a really strong focus on innovation,” Hitt said of the company’s motivation to build Co|Lab. “I’d say the last couple of years we really wanted to transform that into a very collaborative approach, where we are bringing that R&D from a black-box approach out into the open.”
Hitt said the company currently is inviting different groups to take tours of the facility. The goal is ultimately to collaborate with other partner firms to research and develop concepts “to really move the needle in some way,” Hitt said.
Jake Pollack describes a Co|Lab experiment in which augmented reality is pitted against traditional construction:
“That’s one of the beautiful things about the space,” added Jake Pollack, senior project manager at HITT. “We want to engage our subcontractors, our design partners and our clients—but it can really be anybody in the industry.”