Nic Goldsmith, FAIA, LEED AP and Senior Principal at FTL Design Engineering Studio in New York City, is a pioneer in bringing tensile structure design to the United States. These structures utilize exotic materials like Polytetrafluoroethylene (PTFE), also commonly known by the brand name Teflon, and Ethylene Tetrafluoroethylene (ETFE), often seen on professional sports stadium dome roofs.
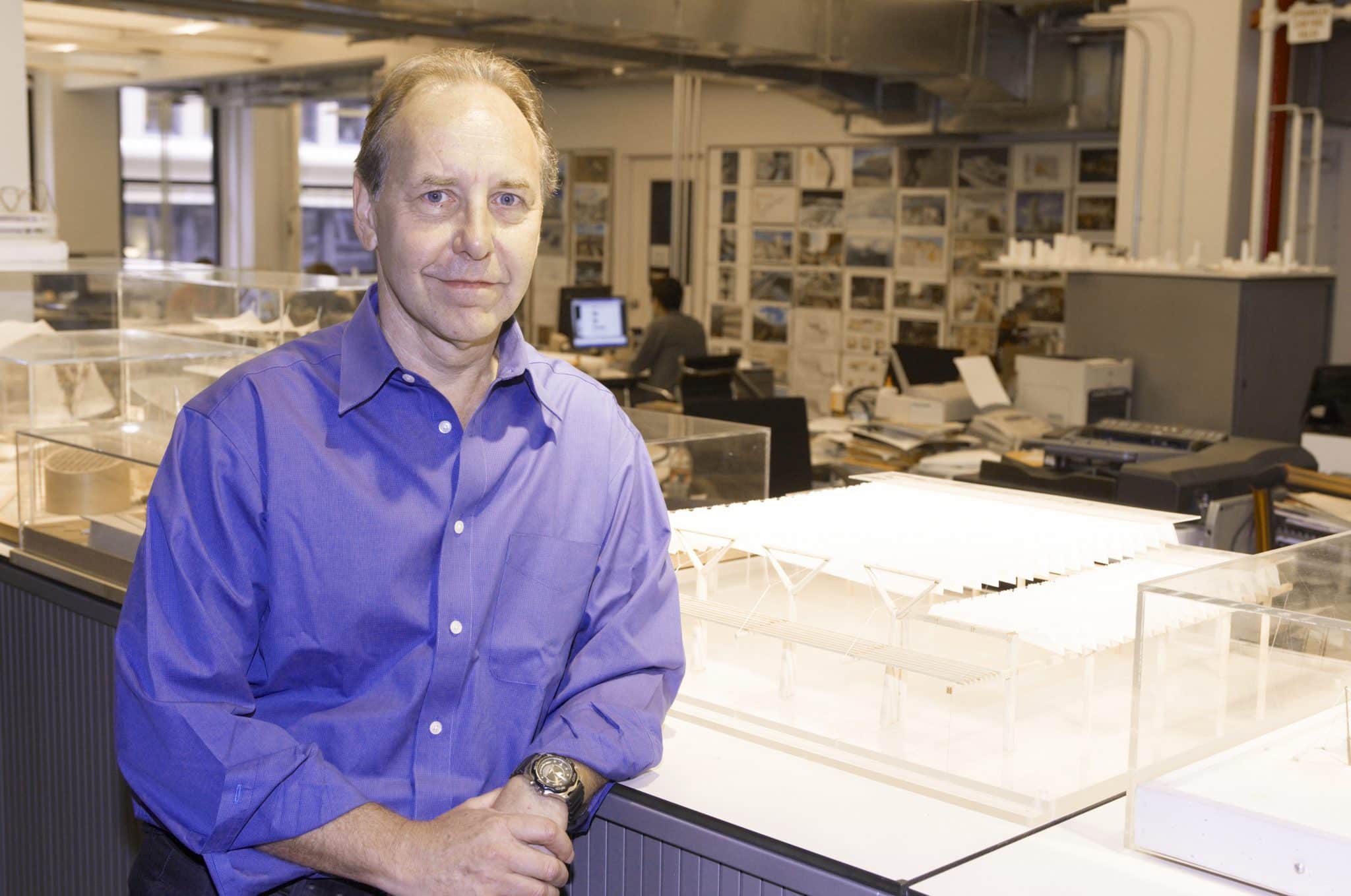
After receiving his tensile structures training under the Pritzker Prize–winning German architect Frei Otto, Goldsmith has gone on to win numerous awards, including the DuPont Benedictus Glass Award and the Excelsior Award for Public Architecture.
The esteemed architect, designer and engineer talked with StrXur to shed some light on designing tensile structures with these build materials.
What did you take away from working with Frei Otto and studying in Germany?
I really understood a sense of something which I hadn’t learned at the university level—and that was this idea of material intelligence. Certain materials just need to be designed in a different way, and understanding how the fabrication process is for each one of those material pieces is crucial. Keep in mind that this was way before we used computer programs, so what Frei used was actually a physical modeling process. Like the famous Barcelona-based architect Antoni Gaudí, we would do those hanging chain models to develop gridshell structures, and each day we’d go in and modify lengths, and the structure would change slowly. It was a very interesting process.
It seems like tensile structures also evolved around giving the public a new look. What other factors or materials spread interest for those designs?
There were software programs that allowed patterning and analysis to go on at a much quicker rate than doing them by hand. Also, people saw a couple of big projects like the Hajj Terminal project in Saudi Arabia, which featured 5.5 million square feet of PTFE fabricated by Birdair. A partner and I did some work with Birdair in the early ‘80s on smaller-scale tensile structures to gain an understanding of how to really develop the form-finding in some of the new digital finite element applications. Those are common today, but back then, they were just starting to be used. We also worked with an English firm, BuroHappold, in the mid–‘80s as they were developing software to gain an understanding of how to create form-finding and patterning analysis programs. Using those new techniques along with PTFE and ETFE were the big steps at the time.
[tweet_dis]“Design is a journey; sometimes you get to a dead end, maybe that dead end becomes a new path.[/tweet_dis] I think that’s one of the surprises in the design process.”
Do you remember the first project you worked on that used ETFE?
The first ETFE project I worked on was in England; we were working on a tennis court cover as a partner with BuroHappold in the early ‘90s. ETFE foil allows a very large spectrum of natural daylight to pass through, unlike glass. It really took a while before the ETFE popularity developed in the States. We did a couple of smaller projects, and in 2012, we did the porte-cochère in Yonkers, New York, a 15,000 square foot structure with Birdair as the lead fabricator on the project. It was one of the first larger-scale projects we’ve done in the States. I’ve seen more and more interest in it since then.
Your firm took home the Excelsior Award for Public Architecture because of your efforts on the Empire City Casino Porte-Cochère. What was the building and planning experience like?
We were working with Studio V Architecture as they were renovating an addition of a casino in Yonkers. They wanted to create an iconic element in the front of this casino to attract customers. We collaborated with them, as they were interested in this ETFE foil/pillow stuff, but the real key was creating something that would allow thirty cars to move in and out underneath it. We started with some freeform pieces but went with a more formed shape. All the radii of the tubes are the same, and we also created more linear elements and different pillows, and we probably saved over 20% of the budget by doing that. It’s a lattice shell structure with inflated pillow cladding and steel frame technology, and even deflated, the pillows could withstand the snow landing, which had to be calculated before sizing it up.
“The more light and elegant you make the shape, the more open it feels and the more it disappears.”
Do you see as much value in ETFE now than when it first began as a building material?
I would consider ETFE to be a growing technology, and I think it has a really interesting future. The modern need for an active shading system is really a wonderful element of this technology; you can actively change the amount of light that comes through the space, which helps for energy use and solar-shading, and it’s minimally more expensive than fixed passive shading. I think it’s a technological wonder, and it’s exciting to be part of something that’s developing basically in front of our eyes. Embedding photovoltaic thin-filmed skin into ETFE fabric membranes can even generate power. That’s an area I see with great potential, but there’s still a lot of development that needs to be done.
As an architect, what made you want to continue working with ETFE and other tensile materials?
One of the things I really like about tensile materials is the efficiency of the material. Using less material is obviously a more efficient way to work; you basically have to get strength not by thickness but by geometry. You have to put curvature and form into these membranes, and there’s a certain beauty to it. Tensile structures can offer a very powerful spatial experience.
Is it satisfying for you as a designer to have played a role as an early pioneer in these tensile structures here in the States?
We will see more and more of these structures wrapped with these amazing foils and skins, and if I can help push it along, then maybe I’ve made a bit of a contribution. For me, it blurs the line a bit between architecture and engineering; we’re architects and engineers. In these types of structures, you can’t really separate the design from the engineering. That goes back again to the whole idea of form-finding; the engineering is a really important part of it.
What still inspires you today? What do you hope the future holds for architecture?
I’m still inspired by this journey of making things lighter and using less materials. Every time we have someone come in from a fabricator firm selling something new, I’m always like, “How can we use this?” To the day I die, there’s always something better or that next step, and I think that’s one of those things that gets you up in the morning and excites you.
Learn more about ETFE here.
*Images courtesy of Paul Warchol.