Suffolk’s Los Angeles office resides on the seventh floor of a seemingly ordinary corporate office building downtown just adjacent to the L.A. Public Library. Inside, roughly 25 employees for the Boston-based general contractor are quietly working.
Clumps of open-office desks sit in the center of a space flanked by a few glass-walled private offices and meeting rooms, connected by a long hallway that bring workers to the kitchen and a second wing. The office design is modern with lots of natural light, featuring expansive views of downtown and the mountain ranges in the distance.
Burrowed in the middle of the office, however, is a sight better associated with a NASA rocket launch or Central Intelligence Agency command center.
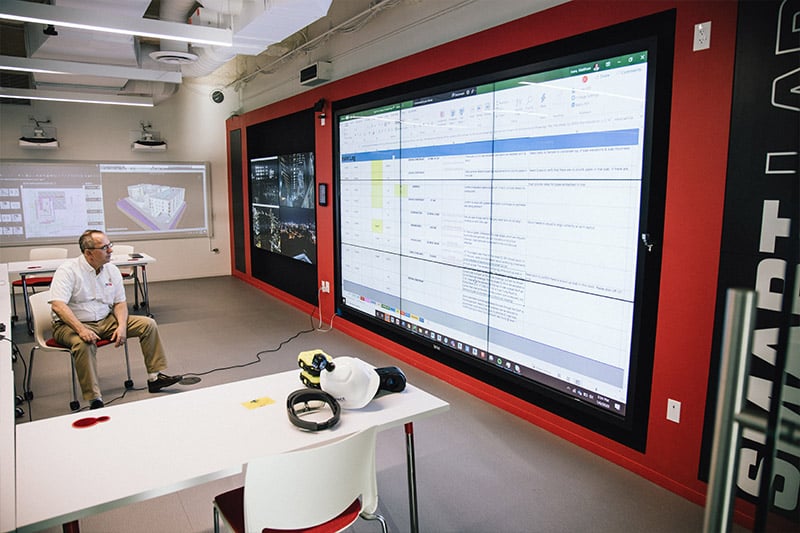
There sits the Suffolk Smart Lab. The approximately 530-square-foot dynamic meeting room stars a nine screen, 12 foot by 7 foot touch-enabled Data Wall; an adjacent sister wall-size monitor with jobsite live streams; as well as a “Huddlewall,” where architects, designers and project stakeholders convene to plan, model and scheme the elements that will eventually translate to the build environment.
Finally, a “Virtual Reality CAVE” sits around the corner from the main Smart Lab space. This is where advanced digital visualization of virtual construction site models and immersive 3D experiences help Suffolk plan pre-construction and site logistics.
The L.A. Smart Lab, which opened in 2019, is one of seven total Smart Labs in different Suffolk offices; the others are in Boston, New York, Miami, Tampa, San Francisco and Dallas.
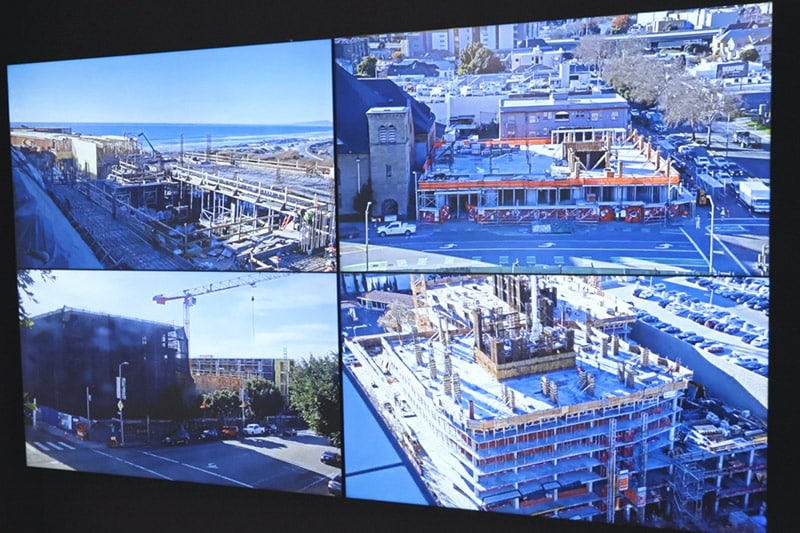
“Traditionally the industry has been pretty slow to adopt technology and innovation as a way of being excellent out in the field and building better,” said Erin Khan, Suffolk’s Smart Lab director for the L.A. office, explaining the motivation behind the company’s wide-scale installation of Smart Labs. “Suffolk CEO John Fish’s vision for the future is about technology and innovation, and we really see that as the vehicle to getting us to a point where we can really be the best builder and be operationally excellent throughout all of Suffolk.”
Khan provided more information about the different components of the Smart Lab.
Data Wall
“There are nine screens that drive the whole thing, so we can pull up nine different things at once if we want to. And then there are also all sorts of different configurations. The idea as well is to be able to pull up information in real-time to have better conversations about our projects, how it’s going and how to solve problems that come up on the jobsite every day.”
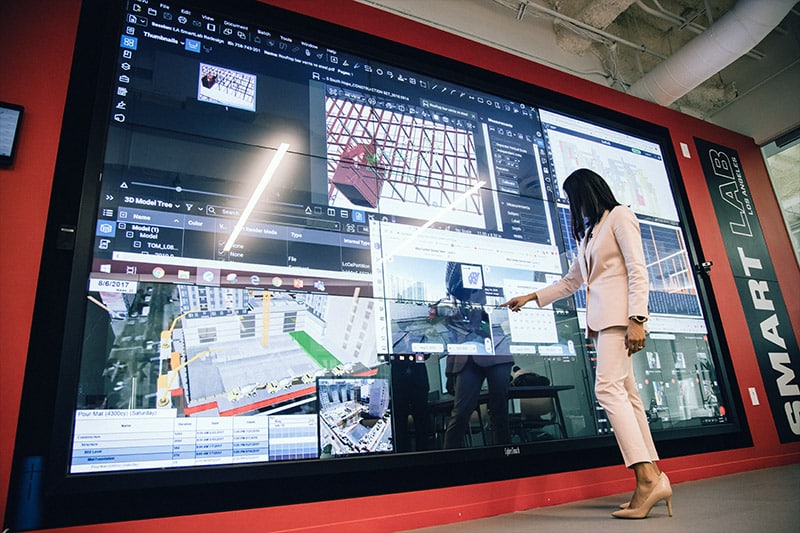
“We have our own in-house data team that manages all these data processes on the back-end through use of things like power BI, Tableau and different business intelligence tools. We’re able to create dashboards that give our teams real-time insight as to what’s happening on the job. If it’s financials or project management related, or employee training for this job—that’s something that we have at our fingertips.”
“Also, with the Data Wall, we can pull up any of the tech tools that we’re piloting. If someone walks in and says, ‘Hey, do you have a solution for site delivery and scheduling logistics?’ We do. We’ve scaled one in particular that’s worked pretty well at Suffolk and it’s just another space to pull that up and show the team, ‘this is what we have that we’ve tried out in other regions. Maybe it’ll fit your project.’”
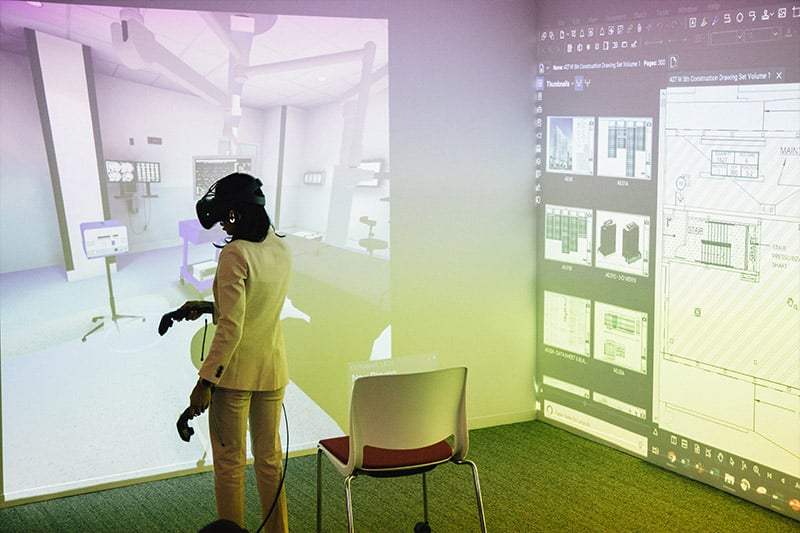
Jobsite feeds
“In the lab we have what we call our two-by-two jobsite feeds, which rotate through different jobs all throughout Suffolk nationally. We can get a national perspective of the types of projects we are working on as well as to see in real-time exactly what’s happening on the jobsite. Some really good use cases for this are obviously safety.”
“Huddlewall”
“Then we have the long ‘Huddlewall’ board, which essentially is a touchscreen and it has special edge-blending technology with the projectors to make it all seamless. We can pull up pretty much anything we like on the boards. But it’s really great for pull planning. The real estate is there so we use a digital pull planning software solution that lets us accomplish real-time lean scheduling with all of the project parties.”

Moving forward
As part of Suffolk’s commitment to bring innovation to the construction industry, the company will soon be rebranding the space from a Smart Lab to a “CoLab.”
Suffolk recently announced it is expanding services beyond construction to include real estate funding, design, technology investment and research and development. The company says its goal behind these new investments is to “continuously reinvent the space to accommodate clients’ current and future needs.”