It’s no secret that innovators often come to their best discoveries in unexpected moments. For Toby McCartney, MacRebur Ltd. co-founder and CEO, inspiration for the technology that would define his career came in an unlikely form.
“The inspiration behind MacRebur began when Toby went to an assembly at his 8-year-old daughter’s school,” said Topher Morrison, the head of MacRebur’s USA division. “The kids were presenting a report to the parents on what lives in the oceans.” Said one kid: “Whales live in the ocean.” Said another: “Dolphins live in the ocean.”
“Toby’s daughter gets up,” Morrison recalled, “and said: ‘Plastics live in our ocean. By the time I’m your age, there will be more plastic in the ocean than animals.’”
“There was this uncomfortable hush in the audience,” Morrison said.
McCartney had what Morrison called “one of those intense dad moments, where he realized that he’s got to do something to prevent that from happening.” For the sake of his daughter and all the other children on stage, McCartney made a commitment to doing what he could to minimize the amount of waste plastics in landfills and oceans. After all, it’s a major environmental problem: an estimated 8 metric tons of plastic enter the ocean every year.
From inspiration to reality
So, what to do with all that plastic?
McCartney remembered past family trips to India, where he had seen locals create temporary pothole filler by chopping up plastic bottles and melting them into bumps on the road, filling the gap with liquid plastic that would then harden into a serviceable road.
Of course, the method, lighting plastic on fire with gasoline, and the results, which were unstable at best, left something to be desired, but it gave him the germ of an idea.
“His concept was to find an environmentally healthy use that could benefit from the non-destructive properties of plastic,” Morrison said. “When you think about plastic, it’s a wonderful thing. It lasts forever. It’s incredibly durable. It’s this incredible product, but that benefit is also its downfall, because the dang thing just doesn’t decompose.”
Watching the Indian neighborhood pothole repair teams gave McCartney insight into the potentially beneficial properties of the much-maligned material. “He realized that you could take this material that has tremendous strength, massive durability … and put it into a product that we want to last for a very long time, like a road,” Morrison said.
McCartney started small by experimenting with chopping up plastic in his garage and using it as a temporary pothole filler. He even got ticketed twice by his local county for doing his experiments in the roadway.
Determined to take things to the next level, McCartney paired up with two friends, co-founders Nick Burnett and Gordon Reed, to enter his concept—which didn’t yet have so much as a working prototype—into Richard Branson’s annual VOOM Innovation Awards. “They went into this pitch with Richard Branson and I’ll be damned if they didn’t win the whole thing,” Morrison said.
The exposure from the competition led to an influx of funding and further rounds of more formal testing that eventually led to a successful formula.
Where the plastic meets the road
One of the MacRebur team’s biggest concerns in developing its formula was ensuring that it wouldn’t create microplastics that would degrade with road use and be recirculated into the plastic food chain.
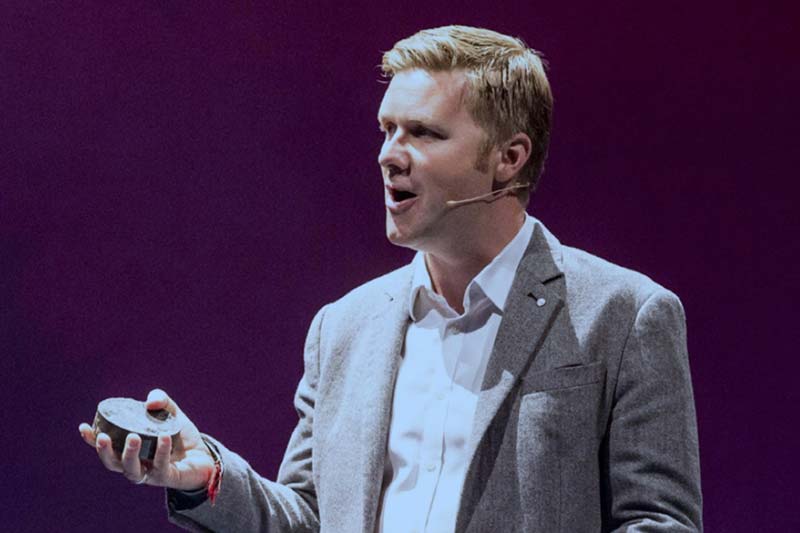
“Toby used his background in chemical engineering to figure out that both plastic and bitumen, which are commonly used as a binder in paving, are petroleum based,” Morrison said. “He knew that he needed to have something which could attach the plastic to the bitumen at a molecular level, and he developed a polymer chain, which when mixed with the waste plastics and the bitumen causes the plastic to homogenize into the bitumen.”
Once you create this kind of solution, the plastic cannot leak out and contaminate the environment. “It’d be like trying to get the cream out of your coffee,” Morrison said. “Once you mix it up, you can’t get it out.”
Replacing part of the standard bitumen mix with waste plastic results in big savings as well as environmental improvements, according to Morrison, who added that the MacRebur blend costs about half of what conventional bitumen costs and performs similarly in real world applications.
“We say plastic roads, but it still very much looks and feels and acts and reacts just like a normal asphalt road,” Morrison said. “We’re able to solve a couple of problems in one swoop. We save asphalt companies money, because we’re taking bitumen, which is a highly valued product, and replacing it with plastic waste, a product that literally has a negative value.”
The resulting product not only prevents waste plastics from going into landfills in the short term, but it transforms them into a recyclable material. “When that road eventually hits its end of life, you can rip that road back up, melt it down and lay it right back down again,” Morrison said.
Easy environmentalism
Morrison said that he’s proud of how easy MacRebur makes it to lessen the environmental impact of a construction or engineering project.
“One of the biggest challenges that most construction firms face when looking at environmentally friendly solutions is that most all green friendly solutions are exponentially more expensive to produce,” Morrison said. “That makes them unviable for most construction firms, because while they want to do the right thing, they can’t cut into their margins so much that there’s no more profit. We are one of the few environmentally friendly products that actually costs less to produce.”
The installation process is also identical to that of traditional asphalt. “There really isn’t any difference in labor,” Morrison said. “It requires no additional technology for the asphalt companies to lay it down. It is simply an additive.”
These simple changes in additive use lead to a big environmental benefit by producing stronger roads that remove disposable plastics from the waste chain.
“Above and beyond all,” Morrison said, “MacRebur is an environmental company. That’s what we’re here to do. Our job is to solve the plastic epidemic. And we have found a solution for taking plastic out of our oceans and out of our landfills and finding a better purpose and a better use for it.”