While the phrase “when in Rome” has become commonplace within modern conversation, “do as the Romans do” rarely refers to anything in the literal sense, but in terms of AEC connotations, maybe it should. While the Romans are credited with a great many influences, it is perhaps that civilization’s dedication to design, engineering and craftsmanship which rises above all else. Historically regarded as “master builders,” the Roman influence on the built environment still stands tall today – much like the very structures they built which spawned such influence. Centuries later, historic buildings like the Roman Colosseum and the Pantheon serve as powerful testaments to the engineering prowess of the forward-thinking civilization. The Pantheon boasts the world’s largest unreinforced concrete dome, quite a feat for a structure that was completed in 128 AD. So what was the Roman secret? An international research team recently found at least a partial answer to that question.
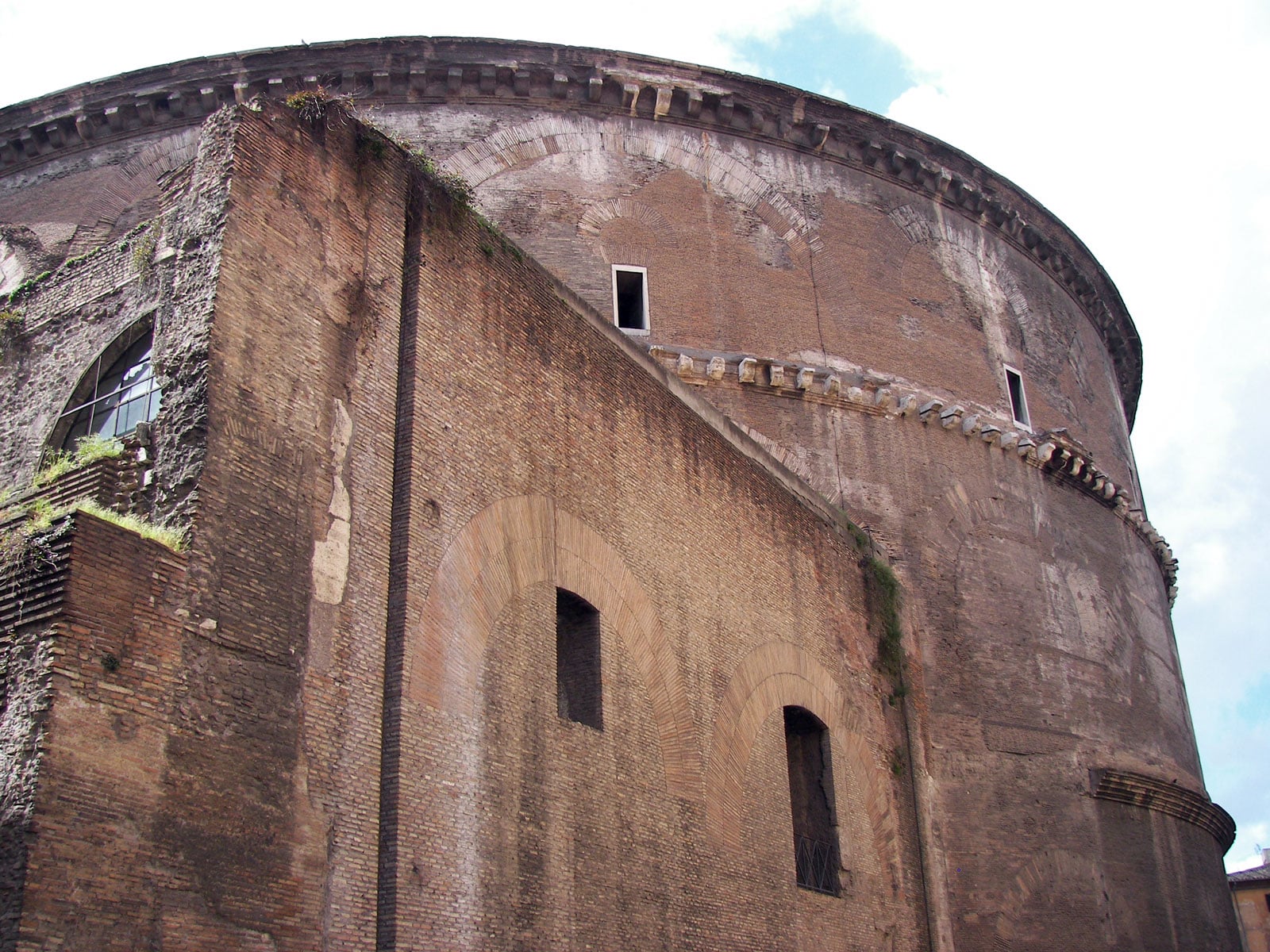
A Concrete Analysis
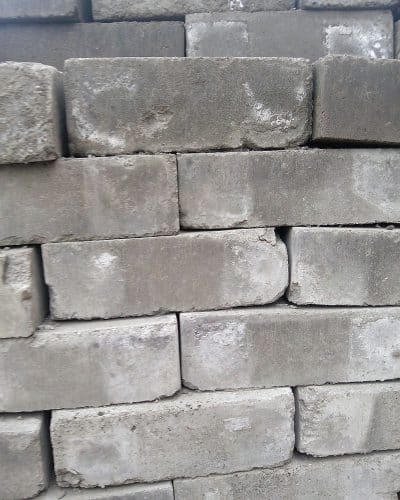
After analyzing the mineral components of an ancient piece of Roman cement, it was determined that the key to Roman cement’s durability lies in mixing lime with volcanic rock indigenous to the area. When exposed to seawater, the mixture forms a calcium-aluminum-silicate-hydrate (C-A-S-H) bond, which yields a robust hardness superior to most forms of concrete. The volcanic rock acts as a supreme mixing agent, or pozzolan, a term derived from Italy’s Pozzuoli Bay. Furthering the benefits of this Roman method, Roman concrete formation requires temperatures in the range of 900 degrees Celsius (1652 Fahrenheit), while the most common form of modern cement, Portland cement, requires hardening temperatures upwards of 1400 degrees Celsius (2552 Fahrenheit). As of 2013, heating the world’s 19 billion ton supply of Portland concrete yields a startling 7% of all human-released carbon into the atmosphere every year.
This epiphany might be spurring a renaissance of sorts within modern concrete production, given the twofold realization that the unparalleled strength of the ancient material is not only too strong to ignore, but the process of creating it may be too sustainable to disregard today.
While the above-mentioned specific pozzolan doesn’t exist worldwide, a few different substitutes have come to the forefront, with fly ash emerging as the most viable option to produce superior concrete.
“If all the fly ash generated each year were used in producing concrete, the reduction in CO2 emissions would be equal to eliminating 25% of the world’s vehicles.”
– National Conference of State Legislatures
Finding the Future with Fly Ash
Created from the process of coal combustion, this naturally occurring material is similar to the volcanic ash in that it yields an extremely high resilience to chemical attacks when used as a bonding agent, and also has a very low level of permeability when used in concrete—making it a stronger and much longer-lasting material than the traditional Portland concrete compound.
Even better, given that fly ash is a widely available waste byproduct of worldwide coal combustion, the impact of using it productively gives it an environmental and cost advantage: For every ton of fly ash used, carbon dioxide emissions are reduced by one ton, and the cost of using the material in concrete is 20%-60% cheaper than Portland concrete, varying by proximity and access to fly ash.
“The cost to build roads, runways and bridges would increase by an estimated $104.6 billion over the next 20 years if fly ash were not available.”
– American Road and Transportation Builders Association
Reducing energy and water consumption, greenhouse gases and costs makes using fly ash a no-brainer in concrete production, and many states have begun to require its use on projects. A briefing paper entitled “Recycling Fly Ash” by the National Conference of State Legislatures states, “If all the fly ash generated each year were used in producing concrete, the reduction in CO2 emissions would be equal to eliminating 25% of the world’s vehicles.” Echoing the material’s overwhelming virtue, the American Road and Transportation Builders Association concluded in September of 2011, “The cost to build roads, runways and bridges would increase by an estimated $104.6 billion over the next 20 years if fly ash were not available.”
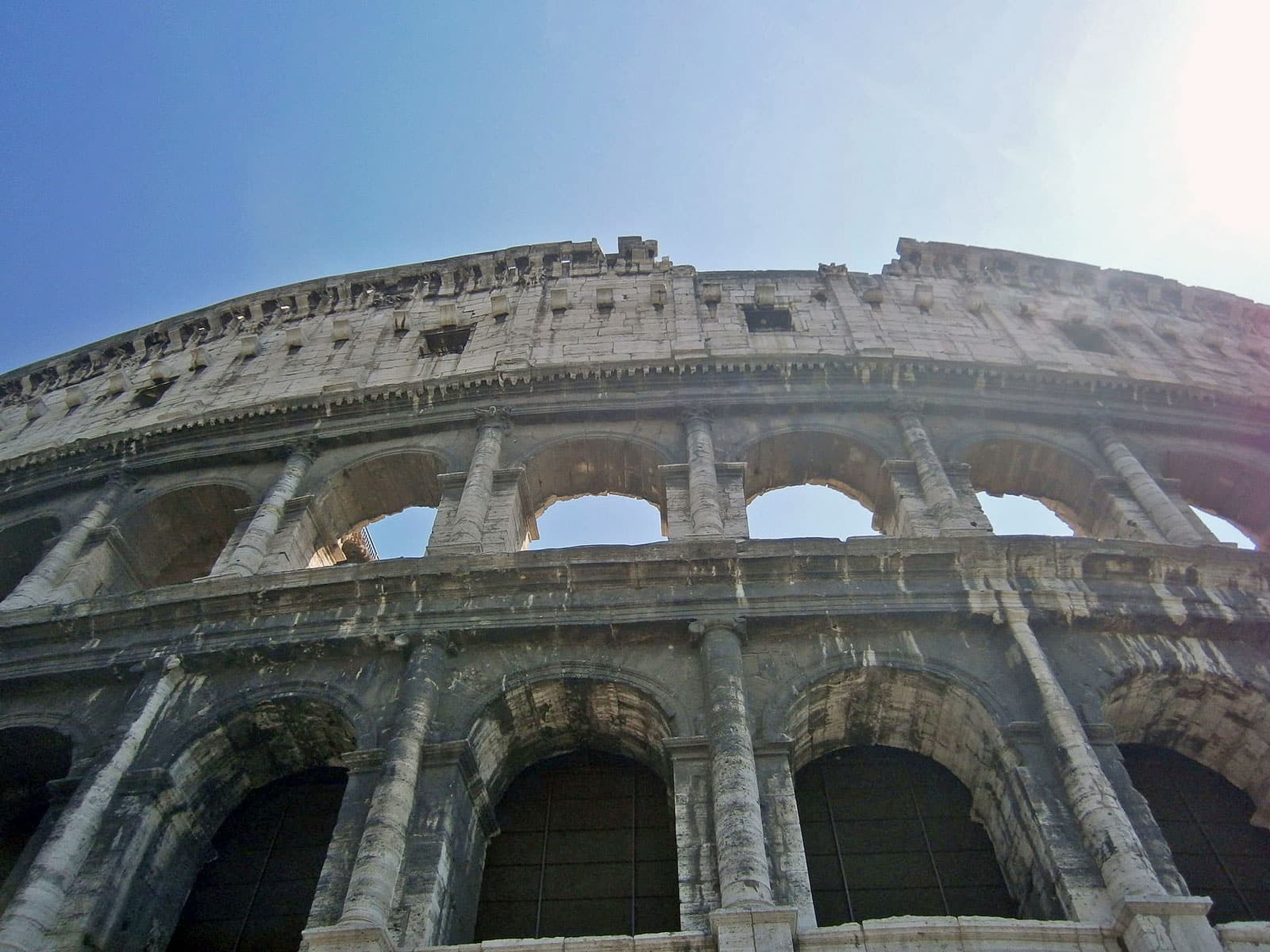
Looking Ahead
Thanks to this mountain of evidence in regard to cost and sustainability, fly ash use in concrete production is increasingly revolutionizing a variety of projects within the AEC industry all across the world. It is not an unreasonable conclusion to credit the analysis of concrete production techniques from an ancient civilization for helping to discover a modern material solution that is stronger, longer-lasting, easier to work with, more environmentally friendly, and cheaper than the previous standard. As the use of fly ash continues to establish itself as a new norm in modern concrete production, it may indeed be true that sometimes you have to look back in order to move forward. Will we find other clues from AEC’s past that help to guide us toward the future? It’s safe to say that in the most literal sense, only time will tell.