In 1842, the city of Mohawk, New York, installed the first concrete sanitary sewer pipe in the United States. Since then, concrete sewage pipes have become the backbone of sanitation systems, with hundreds of thousands of miles in use around the world.
Although the Mohawk pipe was reported in service more than a century later, that’s an exception. Concrete sewer pipes frequently fail in as little as 10 to 20 years, leading to repairs that require ripping up the ground, diverting traffic and disrupting neighborhoods. Annual repair and replacement costs run about $25 billion in the United States and £15-£50 million in the United Kingdom.
The culprit causing failure is the acidic environment in sewage pipes. “Microbes in sewage pipes produce hydrogen sulfide gas,” said Rajeev Roychand, a post-doctoral fellow in civil engineering at the Royal Melbourne Institute of Technology. “This acidic gas combines with moisture to form sulfuric acid, which leaches lime from the concrete and corrodes the sewage pipes.”
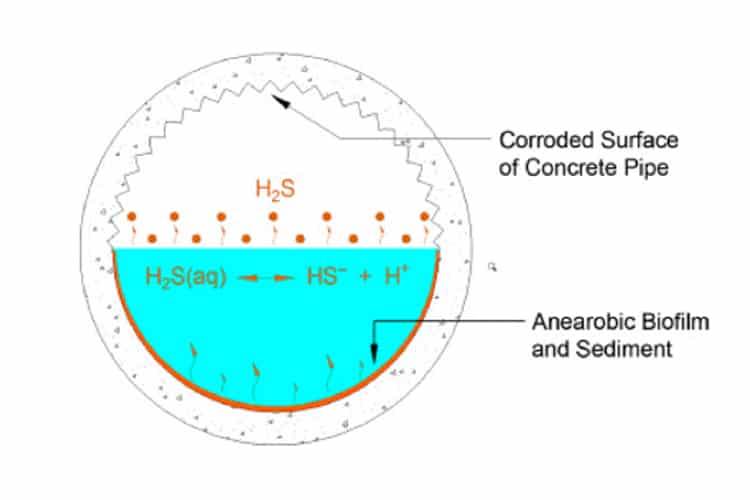
That would be bad enough, but the lime leached from Ordinary Portland Cement (OPC) also contributes to formation of fatbergs that clog sewer pipes. Fatbergs are congealed masses of fats, oils and grease (FOG), combined with flushed materials like wet wipes, that stick to the inside of pipes. And fatbergs live up to their name: One removed from Whitechapel in London in 2017 weighed 130 metric tons and stretched 800 feet.
There’s one more critical issue. The cement and concrete industry contributes to about 5% of total greenhouse gases. Manufacturers are therefore looking for ways to change the composition of cement and make it more energy-efficient.
Recent research by Roychand and colleagues addressed all three of these issues. The result: a zero-cement concrete (ZCC) that meets ASTM strength requirements for concrete sewage pipes, provides durability against corrosion and offers an eco-friendly option to traditional concrete.
Hunt for an OPC replacement
The key to concrete’s strength is calcium silicate hydrate gel. “The normal cement hydration reaction strengthens and solidifies concrete, but also produces some residual lime,” Roychand said. The lime normally stays in the concrete and forms an alkaline coating that protects steel used to reinforce concrete from corrosion. But when acid removes the lime, the concrete pipe thins and weakens.
Adding amorphous silica, like slag, not only consumes excess lime but also creates additional gel. “That increases the concrete strength while totally eliminating the alkalinity,” Roychand explained.
Roychand and his colleagues took a stepwise approach to replacing 70%-100% of the OPC in the concrete with a mixture of other ingredients. The researchers aimed to either minimize or completely eliminate the free lime content.
The two-part study first explored the properties of the raw materials, then evaluated the concrete’s compressive strength and performance in an aggressive acidic environment.
Raw materials for success
Making the cement more environmentally friendly was a top priority. Other approaches have included use of alternative fuels and either blending cement or replacing conventional aggregates with industrial by-products. In fact, the portion of blended cement manufactured has increased significantly in recent years, as the construction industry has become more aware of greenhouse gas impacts.
From earlier research, Roychand and his colleagues settled on several materials to investigate. The first three all reacted with lime to form additional calcium silicate hydrate gel:
- Fly-ash – a silica byproduct of coal combustion
- Slag – a glass-like by-product of steel smelting used as an aggregate in concrete
- Nano-silica – a particularly reactive form of silica due to its small particle size
- Calcium hydroxide – an external source of lime that ensures the reaction continues
The researchers used X-ray and thermal analyses to establish the physical, chemical and mechanical properties of trial cement composites and scanning electron microscopy to evaluate the concrete microstructure. “Combined, the analyses gave us a clear picture of the reactions and the products that were forming and how they increased the strength properties,” Roychand said.
Stronger and longer-lasting concrete
The research team’s tests for compressive strength confirmed that the ZCC’s mechanical properties met ASTM requirements. Next came the test for acid attack durability to assess corrosion performance.
Previous research into the acidity in sewage environments found the pH varied between 7.2 (like tap water) at the bottom and 2.9 (about like grapefruit juice) at the top of the pipe. But corrosion occurs slowly over years.
Roychand and his team used a much more acidic pH of .2 pH to accelerate the process. “If we had gone with the acidity present in sewage pipes, it would have taken me about a decade to do one experiment,” Roychand said.
After allowing the concrete to corrode for two months, the researchers determined that the ZCC reduced corrosion by 96%. The higher the lime content in the concrete, the faster the deterioration when exposed to the acidic environment.
Pictured Above (from left to right): Conventional cement concrete after 56 days in an acid solution, showing loose matter and froth formation resulting from reaction of acid with lime; same sample after cleaning and drying; and ZCC after 56 days in an acid solution.
A solid future
To make the ZCC more marketable, the researchers removed nanosilica from the mixture. “With more cost-effective materials to replace nanosilica, the concrete has become much more interesting to the concrete industry,” Roychand said.
In fact, the ZCC overcomes all three major issues created by use of conventional concrete. “You get similar strengths, it’s economical and you cut down on environmental emissions,” Roychand said.
Moving forward, the research team plans to examine other areas of major infrastructure investment, such as marine environments, where materials are also prone to corrosion.
*Development of zero cement composite for the protection of concrete sewage pipes from corrosion and fatbergs” is published in Resources, Conservation & Recycling (DOI: 10.1016/j.resconrec.2020.105166)