In the opening scenes of Mike Nichols’ legendary 1967 film “The Graduate,” Benjamin Braddock, the film’s eponymous anti-hero, is at a loss concerning his future. A friend of the Braddock family and local businessman, Mr. Robinson, tries to help, enthusiastically giving the youngster a piece of advice: “There is a great future in plastics. Think about it. Will you think about it?” Without any enthusiasm, Benjamin replies that he will.
Looking back half a century ago, it’s almost quaint to consider that a material we now find so commonplace was regarded as a nascent technology. Back then, new things were being made with plastic, offering unparalleled convenience and countless opportunities to do things differently. It was, as Mr. Robinson stressed in the film, the future.
Today, the picture is quite different. Rather than convenience, for many the word “plastic” is more likely to be synonymous with waste and environmental catastrophe. It’s easy to see why.
According to environmental group Plastics Ocean International, more than 300 million tons of waste plastic are generated worldwide every year, and as much as 8 million tons of this waste ends up in the world’s oceans annually. What all that means for the wildlife that makes the seas their home is now being highly publicized by the likes of naturalist Sir David Attenborough and others.
While there is clearly a plastic waste problem, strenuous efforts are being made to contain the spiral of debris that blots landscapes and marine environments all over the world.
And as much as we should do all we can to address this issue, it is worth remembering that plastic is more than an image of a single-use water bottle floating forlornly down a river or a discarded plastic shopping bag being lifted high into the air on an autumnal breeze.
Plastics used in construction: A very suitable material
Used—and indeed disposed of—wisely, plastic is still very much the boon material it was in the 1960s (more so, in fact). Advances in technology mean that plastic materials are considerably lighter than their metallic counterparts, and thanks to new additives, they can be applied to a wider range of end uses, including medical, packaging, automotive and, of course, construction.
When one thinks about plastics used in construction, things like pipes, drainage systems and guttering spring to mind. And with good reason. The weight of such parts made from plastic is much less than the metal fixtures that were used before. The speed with which such systems can be installed is another advantage.
For example, Polypipe, a U.K. company that produces plastic piping and drainage systems for the construction industry, designed and supplied a complete drainage network for Southampton City Council to replace existing cast-iron pipework on a 240-foot-high residential tower block.
Thanks to the composition of the system, it was able to be installed in 40% less time than was the average for such works.
And while it is useful in the “nuts and bolts” of a building, plastics in construction have moved into new territory. Innovation and advances in material technology and, crucially, recycling mean that plastic can be put to uses in both buildings and infrastructure, end-markets unthinkable half a century ago.
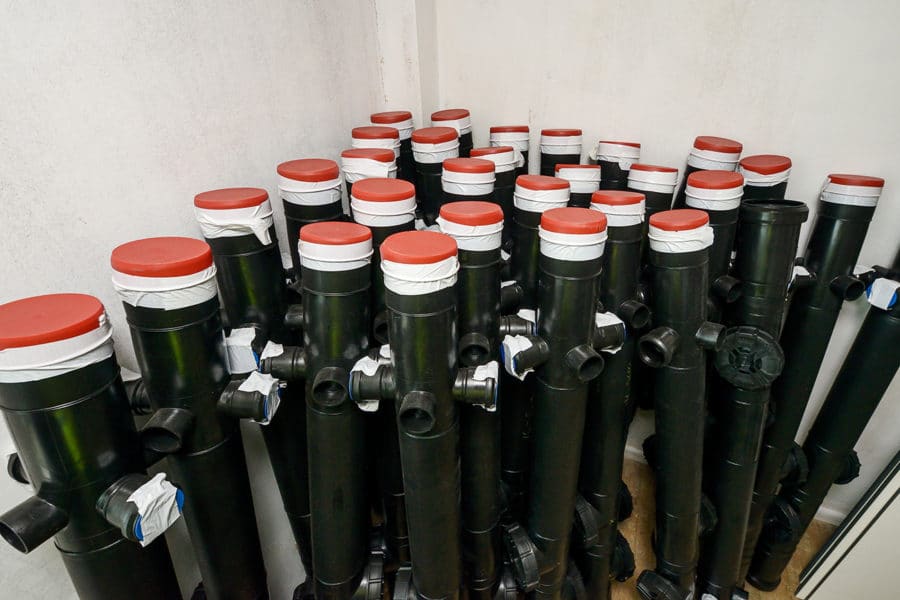
A myriad of uses
It can help in moves toward a low-carbon economy, particularly with new bio-based resins replacing oil-derived plastics. And when it has been used and is ready for disposal, it can be turned into new products.
Take highways. Entrepreneurs around the world have developed methods to turn non-recyclable waste plastic into road surface material.
One such outfit, MacRebur, based in Lockerbie, Scotland, claims that for every kilometer of six-meter-wide road laid using its MR product—which is added to bitumen to extend its range—it uses up the equivalent weight of nearly 741,000 single-use plastic bags, while one ton of MacRebur mix contains the equivalent of 80,000 plastic bottles, a massive step for plastics in construction.
Then there is the 30-meter-long plastic bridge spanning the River Tweed near East Dawyck, which is made entirely of reconstituted plastic waste, developed by U.K. firm Vertech Composites.
And while new technologies seek to find alternative uses for general plastic waste, the construction industry itself generates a considerable amount of the stuff through using things like shrink-wrap and other products to transport materials to sites.
Yet here, too, plastic is making inroads, dealing with the problem by re-using packaging where possible and submitting non-reusable plastic for recycling.
Plastic buildings
But lest you think it’s just about ways to create a circular economy for plastics in construction, think again. The sector is becoming more open to designing structures that incorporate plastic in their fabric. Sometimes such structures do more than merely incorporate; they are made wholly out of plastic.
The 2015 Serpentine Pavilion, for example, designed by Spanish architects Selgascano, was an amorphous, double-skinned polygonal structure consisting of panels of a translucent, multi-colored fluorine-based polymer, woven through and wrapped like webbing.
Yes, the pavilion five years ago was a temporary structure, designed to be both eye-catching and perhaps a tad controversial. But like other such one-off designs, it points to what can be achieved with the material. It explores the possibilities of plastics in construction.
Other buildings use plastic more integrally. Plastic has been used in insulation for years, and a decade ago, an architecture firm in Poland designed a house clad in a material called Thermopian, which is normally used for roofing.
The firm, Moomoo, said Thermopian had good thermal, acoustic and insulating properties and could be installed in any color a client wished.
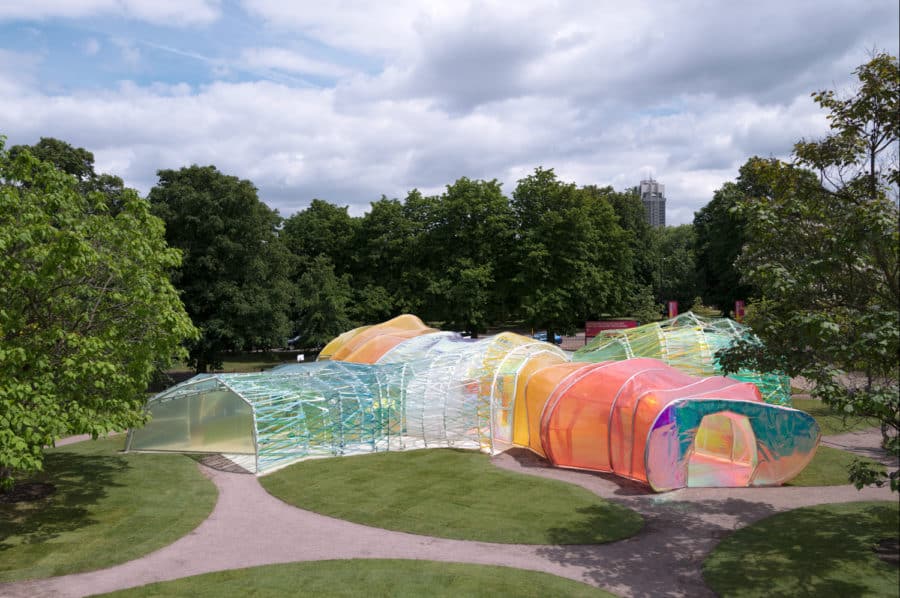
Versatility and durability
The plastics industry has always had a close affinity with the construction sector, and in the U.K. a number of manufacturers of plastic products are members of the British Plastics Federation (BPF), which seeks to promote the material wherever it can and counts the likes of Polypipe and others among its ranks.
The BPF’s director general, Philip Law, is understandably upbeat about his industry’s relationship with the building sector.
“Due to their versatility and durability, plastics play an undeniably essential role in construction and we see continuous innovation in this area,” Law said. “Plastics are critical to infrastructure renewal, either built or digital.”
“Their insulation properties, leading to greater energy efficiency, put plastics at the forefront of decarbonisation,” he added.
So as Mr. Robinson said, plastics in construction really is the future. Benjamin, take note.