In a recent customer survey, Australia’s leading construction firms revealed which workflows they’ve seen the biggest improvements in since going digital. Their five most-improved workflows—design review, quantity takeoff, RFI management, drawing management and site logistics—span the entire project lifecycle.
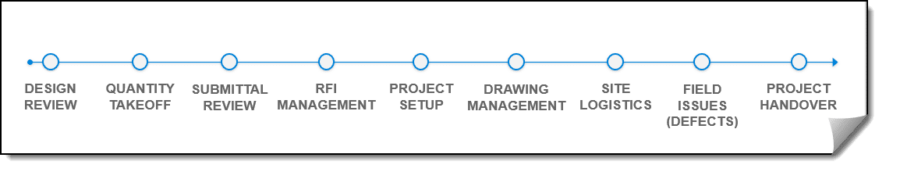
General contractors, sub-contractors, architects, engineers and owners who are in constant collaboration throughout the project have historically relied on paper to get the job done. Those who have transitioned to digital workflows are finding greater efficiencies and consistency, not to mention helping the environment by reducing printed paper.
To demonstrate how easily businesses of any size can achieve the same efficiency gains, we recently hosted a five-part “Back to Basics: Revu for Construction” webinar series. Here’s what we covered.
Episode 1: Handling and Editing PDFs
PDF drawing management may seem like a staple requirement, but not all PDF editing software is created equal. Revu was purpose-built for construction, supporting large-format PDFs and providing industry-specific communication tools.
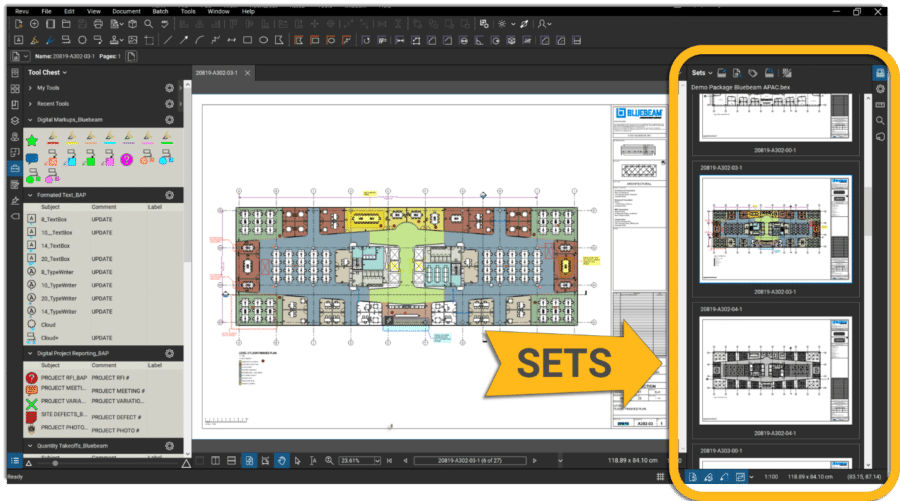
Key Lessons
- Combining drawings into a single file and using Batch Slip Sheet
- Keeping drawings separate and using Sets
- Creating a Studio Project with Sets on Projects for all to access
- Creating a Studio Session for communicating anywhere, anytime
If I had to pick my two favourites in this list, it would be Sets and Studio Sessions. I haven’t seen anything else with such simple steps that can save so much time.
Sets
Sets replaces the use of a “current folder” on a desktop or shared folder to an interconnecting, hyperlinked document management system (DMS) that automates the latest drawing onto the Set. It includes all the project drawings from every consultant, and, most important, brings all the markups or data from previous revisions onto the latest drawings.
We are seeing the growth in data onsite, and our customers who migrate from paper to digital workflows in construction find that their common markups are valuable digital information.
Studio Sessions
I understand some people think moving information to the cloud can be daunting, but think back to when you came back from a holiday and went to the chemist to print your photos. Now we upload our photos directly to social media while we’re away, our friends comment and we comment back. Most people use digital processes in their personal life, and it’s not such a big leap to adopt similar workflows at work. With little training, construction teams are digitising their workflows in tender and design reviews, value management, shop drawings, and site tracking. The ability to be anywhere, anytime, for a collaborative process has saved our customers many hours of valuable time.
Episode 2: Reviewing and Signing Digital Documents
This is a game-changer in construction.
In this webinar, we showed the ins and outs of using Revu to create digital forms and signatures, and make sure all reviewed documents are secure. For those who need to improve consistency in documentation, Revu enables you to create your own standardised processes.
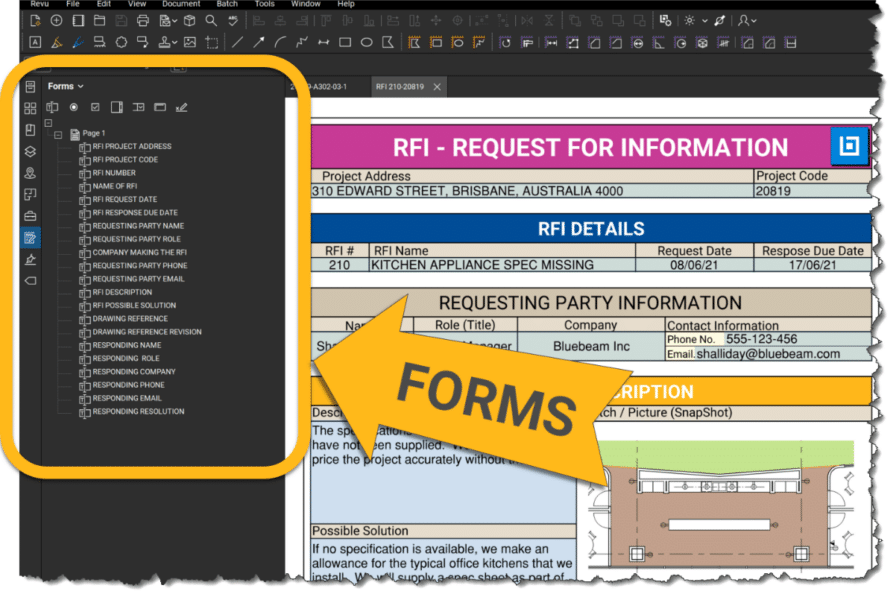
Key Lessons
- Completing forms with Revu
- Creating templates
- Signing documents
- Certifying documents
Templates that use Forms
The draftsperson in me loves to use Forms and Templates for everything from recreating CAD drawing titleblocks and RFI documents to signing my kids’ school permission notices. Once a Revu Form is set up, it’s as easy to use as any form you’ve filled out online. There’s also opportunity to add radio buttons, text boxes and multiple-choice dropdowns, among other features. If you want to step it up to another level, you can use coding (JavaScript) in the background to automate tasks, turn sections on/off and the list goes on.
Check out this support article for more on JavaScript in Revu.
Episode 3: Standardising Tools and Processes
In any construction or engineering project, there will be multiple workflows happening at once. The good news is that Revu can help you digitise these workflows and standardise processes just as it has for so many customers around the world.
If you’re using Revu, you’re already halfway there. It’s now about using Tool Chests, Custom Columns and Statuses to build a Revu Profile that can be shared.
In this webinar episode, we explored digitising construction projects and raising the productivity and efficiency of work across the board with Revu. Consistency is key to running any project effectively.
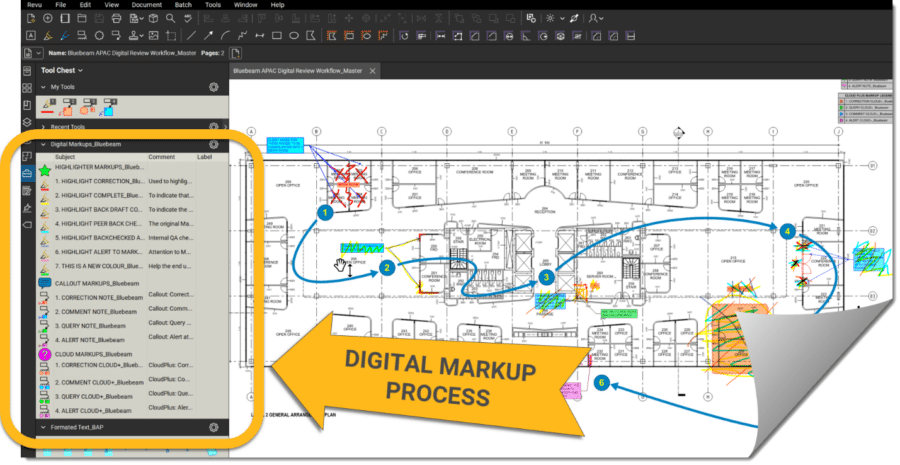
Key Lessons
- Migrating paper markup workflows into digital workflows
- Status Workflow, where the original markup is colour-coded
- Studio Sessions, collaborating anywhere, anytime
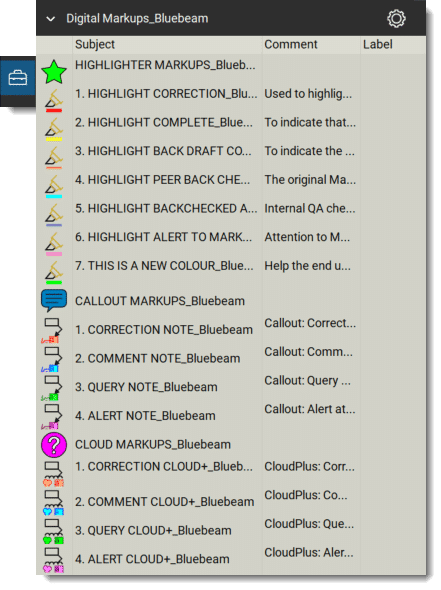
While combining these three key lessons provides the best results, each topic offers a significant improvement of its own.
Throughout this webinar series, I talk a lot about setting standards through Tool Chests because it is the easiest way to transition to digital processes. Then with the power of Statuses, users can change the colour and create historic data about their markups. For example, ”Door to be demolished and replaced with …” could be marked up in red; then, using Statuses, change the markup to yellow when it’s been drafted, orange for backchecks and then purple for QA review.
Lastly, all information can be uploaded to the cloud with Studio Sessions, and all staff, consultants and stakeholders can collaborate and communicate live on the same PDF files.
Episode 4: Streamlining Quantity Takeoffs
Getting the correct measurements and counts is a crucial and complicated part of any build. Revu streamlines the process by digitising paper workflows and combining spreadsheets into one tool to provide you with accurate quantity takeoffs.
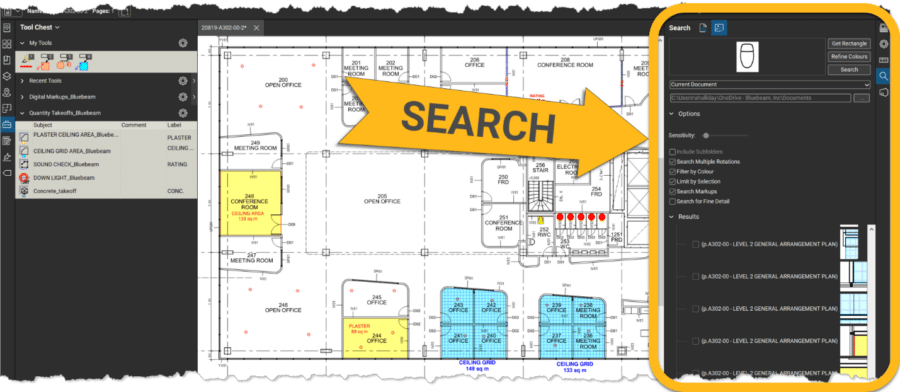
The key to success is the standardisation of Tool Chests, Custom Column creation and consolidating these elements into Revu Profiles, which we discussed in Episode 3. In this webinar, we looked at how our customers are doing this for quantity takeoffs.
Key Lessons
- Setting the scale of drawings in Revu 20
- Using the new custom tools for Linetypes
- Measure steel rafters for a building—adding the size and weight
- Count tool for MEP diffusers
- Quantity takeoff by combining the Search and Count tool
- Concrete takeoff by using the Volume tools
- Overlay and compare differences between drawings
It’s difficult to pick a few points from the key lessons above as they are all part of one larger digital construction workflow. I refer to a painter in South Australia who I helped to set up a Revu Profile.
Use Case: Painter, South Australia
I walked in and immediately saw these A2 plan drawings with different coloured highlighter marks and hand-marked-up hatch patterns. The system was so easy to migrate from paper to digital, improving upon the workflow this painter depended on for the past 30 years. We built a Tool Chest, Custom Columns, and Layers as a workflow foundation. Then when updated drawing revisions came in, using Overlays made it easier to pick out unclouded design changes and use the Search and Count tools to count variations.
The painter was able to use the Overlay workflow to discover new ceiling openings, find each one on all levels of a building with Search and then use the Count tool to calculate a quantity. Lastly, we created a PDF report of his variation to the builder—all in Revu.
Episode 5: Managing Site Logistics
In our final episode, we looked at how any building site has a vast number of elements to keep track of at once. Bluebeam Revu can handle the many logistical challenges of a build, saving you time, effort and resources in the long run.
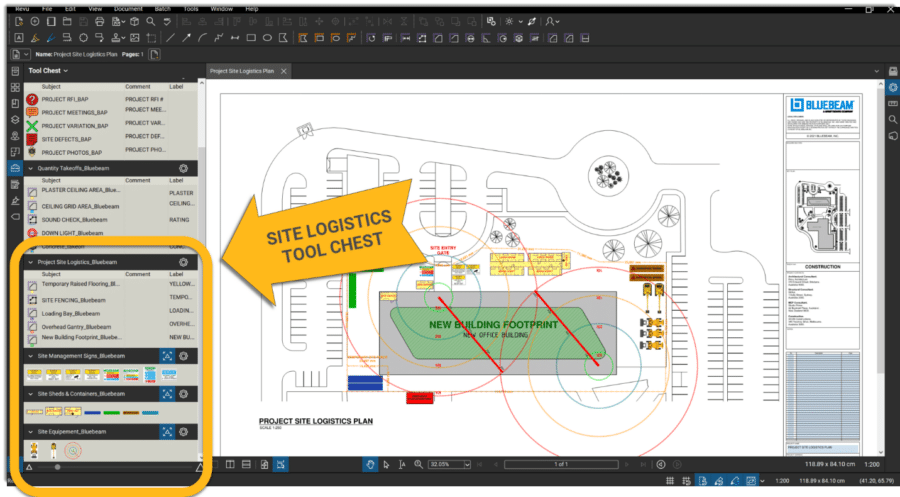
In this webinar, we created site logistic plans and content in Revu Tool Chests and shared Site Logistics Plans across projects so that everyone on- and off-site can keep track of current site management.
Key Lessons
- Creating a Revu Template with Forms for a Project Titleblock
- Creating site plans using Google Maps or Near Map
- Adding in temporary fencing, safety walkways, site sheds, signage, crane, etc.
- How Site Logistics Plans can be shared with Studio Sessions
Creating Site Plans with Map Data
I picked these two items from the key lessons because they often have the greatest impact. I’ve seen some complicated methods including MS Paint, Excel or overpowered CAD tools. In this episode, I demonstrate an easily replicated method that is used by many of our customers to build and distribute information and updates to the entire site team. Just another example of great digital workflows for construction.
Series Wrap-Up
Adopting digital workflows doesn’t have to be a daunting process, as it builds upon the same workflows you may have been using for decades. Going digital for a construction company is not always a big jump into drones or 3D models—there are smaller steps within reach. Simply moving these five key workflows from paper or software that isn’t intended for the construction industry to purpose-built software like Revu will have a significant impact.
To find out more about the benefits of adopting digital workflows in construction, you can view the five-part webinar series recordings via the button below.