Hoffman Building Technologies (HBT) is in the business of making buildings new and old run more efficiently.
The North Carolina-based company’s core business is building automation, which covers everything from lighting, HVAC and HPAC controls to energy, gas and water management.
Launched in 1985 as the controls division of Hoffman and Hoffman, HBT’s systems can be found in more than 1,000 buildings across Virginia and North and South Carolina.
But even as its clients reaped savings from the latest in building automation, HBT increasingly found its internal processes for everything from sharing documents to making changes in the field weighed down by a traditional reliance on paper documentation.
Two years ago, some members of the HBT sales team began experimenting with Bluebeam and were impressed with its capabilities.
In early 2020, HBT launched a pilot program aimed at converting the rest of the company to Bluebeam Revu for project and document management.
Just a little more than a year later, the results have been dramatic.
HBT has completely transformed the way it works, with the company’s engineers and technicians having shed cumbersome paper documentation in favor of seamless digital collaboration using Bluebeam Revu.
It has also been a win for customers, further boosting the already high quality of the company’s work and services, said Chris Stegall, HBT’s vice president of operations, who gave the green light for the rollout of Bluebeam across the company.
“Everybody is on the same page,” Stegall said. “We have less risk of maybe things slipping through the cracks because it’s done pretty much instantaneously.”
How it all began
An engineer was the first person who began using Bluebeam Studio in Revu, said Patrick Gorman, HBT’s operations supervisor in the firm’s Raleigh, North Carolina, office. Gorman has played a central role in championing the new technology.
Based in Charlotte, the engineer had been working with a client who had documentation requirements and had been trying different things, including BIM 360, Microsoft Excel and Access, as he explored the best way of storing data as well as exchanging it with staff in the field.
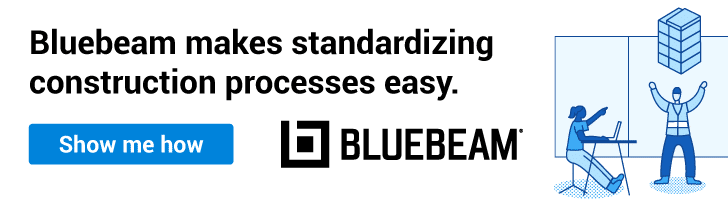
In the process, he came across Bluebeam Studio in Revu, started using it and began having success meeting the client’s requirements with it.
Catching wind of what the engineer was doing, Gorman said he quickly saw great potential in Bluebeam Studio’s cloud technology and took over the vetting process.
Roughly 75% of HBT’s work involved printing off and storing paper documents, a time-consuming process that requires significant storage space.
Yet it was the company’s reliance on a virtual private network (VPN) connection to transfer data from worksites back into a company server that proved to be the straw the broke the camel’s back.
“Working in the field, having to deal with a VPN connection back to something, you had to have a pretty stable connection,” Gorman said.
So Gorman began work with one of his engineers on ways to “design and develop a structure” for the rollout of Bluebeam’s technology across the company.
It was the start of a two-year journey that would transform the way HBT communicates and tracks projects.
[RELATED VIDEO: 4 Strategies Construction Firms Can Use When Adopting New Tech]
“The aim was to have something that could be “easily rolled out, easily trained and literally easily used,” Gorman said. “I’m a firm believer that if you have a tool that’s not easy to use, you’re less likely to use it, regardless of what that is.”
Gorman and his team spent “the better part of a year” experimenting with Bluebeam Studio when their work came up during an internal review with Stegall, who suggested they present their findings at the semi-annual managers conference.
“We had a lot of buy-in, a lot of questions from the other project managers,” Gorman said.
Soon, Gorman and other members of his team were working on developing a training curriculum to pave the way for a rollout of Bluebeam Revu across the company, with the help of construction technology training firm TPM Inc.
Gorman set up two training classes—one in South Carolina, the other in North Carolina—and started with the company’s project managers before moving on to the firm’s technicians and engineers.
The aim was to ensure “everybody from top to bottom would use the process,” Gorman said.
When a job is booked, the project manager oversees collecting everything that’s needed including “the mechanical plans, electrical plans, specifications, the scope,” Gorman said.
As part of their training, project managers learned that their first step now is to create a Studio Project, Revu’s document storage capability, for the job, effectively establishing a template for the folders made for each job.
“And then you just start dropping in the data into the folders where it would normally be,” Gorman said.
Gorman, in turn, has continued the training as the company has ramped up its digital capabilities with Bluebeam.
He is now working on helping staff in the field become proficient using Studio Sessions, Revu’s digital collaboration capability, on their iPads, while helping HBT’s engineers understand what Bluebeam is for.
“We spent two years perfecting it and getting to the point where we, one, understood Bluebeam enough, and then two, develop the process to roll it out to our people,” Gorman said.
Sweeping transformation
All of which represents a sea change from how HBT operated before Bluebeam, Gorman said.
Engineers spent much time and effort preparing project booklets in three-ring binders to give to the company’s technicians.
That involved a large amount of paper and printing, including mechanical and electrical drawings and control and checkout documentation for equipment.
“And that was the way Hoffman had done it for years,” Gorman said. “We literally had shelves in our storage of the three-ring binders from all of these projects where this information was.”
Communication and collaboration between different offices and with staff out in the field has also become simpler and more efficient.
Using Bluebeam Studio, engineers take all the information gathered by the project manager and then start developing the control and equipment submittals, among other things.
The engineer can then upload their PDF files to a Studio Session within Revu, send out invitations and let the markups begin, with everyone working off the same document if the Session is active. Everyone on the team has access to the same documents through their iPad, laptop or phone.
Gone is the time-consuming back-and-forth exchange of proposed changes and documents.
“That has been a large—I mean, an astronomical improvement on our process by reducing time spent reviewing documents with 4-5 different people,” Gorman said. “Now, with Sessions, it’s very quick, done within days, and there’s no back-and-forth traffic.”
HBT’s use of Bluebeam Studio has also streamlined communication between technicians in the field and staff back in the office over checkout documentation, change orders, RFIs and many other things.
At “any given time, our technician in the field, our project manager, anybody, can say, ‘Hey, I’m John Doe, contractor here. What’s the deal with this change order? What’s that? Are we done? What are you waiting on?’” Gorman said.
Improved billing
Bluebeam has also helped make the billing process more efficient.
General contractors often require a monthly as-built invoice to get paid.
Previously, when it was all done on paper, the technician would have to bring the book to the engineer, with the technician unable to continue working while the updates are being made, Gorman said.
Now all it takes is a simple email to the engineer asking for the updates on the as-builts for a particular job number.
“He quickly goes right to Bluebeam Studio, confirms with the technician, ‘Hey, I am pulling a copy of the red lines to make as-builts,’” Gorman said. “Therefore, [the engineer] makes his updates, posts the as-builts, I can go ahead and quickly get paid, and it takes seconds.”
Another potential problem with the old paper-based system was that folders got misplaced and documents lost.
[SEE MORE: What Contractors Need to Know About Volatile Materials Prices]
It was a particularly big problem when the item lost or misplaced was the check test documentation, which consisted of a paper spreadsheet stashed in a larger book of documents.
Gorman said that check test documentation is “where we verify every single wire, every single device, they have to sign off on it.”
“Well, if the book got lost halfway through the project, everything that you had documented is now lost,” Gorman said.
Today, that crucial documentation is stored electronically in Studio. In addition, the project manager or whoever is working on the document can check it out, preventing anyone else from making a change while it’s being worked on.
“So everything about it, every aspect of using it, has added a benefit to us,” Gorman said.
Maybe one of the biggest benefits has been the buy-in and enthusiasm for Bluebeam Revu on the part of technicians, engineers, project managers and others at the company, Stegall said.
In particular, he cited the software’s interface and its ease of use.
That isn’t often the case when it comes to rolling out new technology, with some employees preferring the comfort that comes with the old way of doing things, he said.
“It definitely allowed the buy-in to be quicker,” Stegall said. “And so this has been very much a pleasant surprise to see the team come together, embrace it and have a little bit of excitement with regard to what the next step may offer HBT in general, with how we conduct business.”