StrXur spoke with Zachary Podkaminer, director of strategic initiatives at Construction Robotics, about their new jobsite technology called SAM. SAM—which stands for Semi-Automated Mason—is a robot capable of laying over 2,000 to 3,000 bricks per eight hours, four to six times what a human can do. Podkaminer talked about efficiency, the labor shortage, whether robots will eventually replace humans on the jobsite, and how SAM will change the way the industry thinks about process.
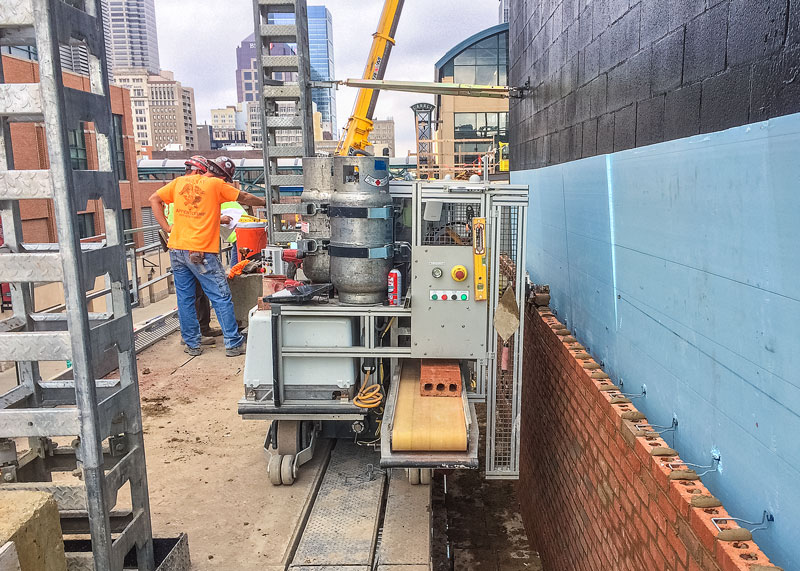
StrXur: A hot topic in the AEC industry is the labor shortage. How does SAM play a role in this?
Zachary Podkaminer: We keep talking about a labor shortage, but if you look at manufacturing and their employment over the past 20 years, it’s pretty much stayed the same or declined. At the same time, their productivity has significantly increased, and that’s because they’ve implemented technology to make their production line more efficient. Same thing in construction: a labor shortage could just be a symptom and one way to solve the issue is to make labor more efficient.
StrXur: So what’s the role of robotics in this?Podkaminer: It’s simple. We don’t see construction, especially on-site construction, ever being fully automated. There’s too much variance. Everything is dynamic and it’s not a controlled environment, so we’re beginning to see construction and automation equipment being leveraged by workers to make them more efficient. Workers will always be part of the equation. What SAM does is amplify the workforce: If you have two masons and a laborer working with SAM, instead of getting somewhere between 300 and 500 bricks a day per man, now your two masons can get anywhere between 2,000 and 3,000 bricks in eight hours. The masons can focus on quality, and SAM can take away the heavy lifting.
StrXur: Does SAM affect workplace safety?
Podkaminer: Absolutely. The majority of injures in construction are back injuries. And it’s from the repetitive wear and tear on the body. So whether it’s SAM or MULE [Material Unit Lift Enhancer, a lift assist device also created by Construction Robotics] our concepts are to make the workplace a healthier and more efficient and safer environment. By allowing the workers to do less of this repetitive heavy lifting, they’re going to be less prone to injury.
On top of that, if I were to show you a picture of two jobsites, one with a regular crew and one with a SAM crew, you’d see a stark difference. When you look at the one with the SAM crew you’ve got your cubes of brick, you’ve got your mortar bucket, and you’ve got three workers and a robot. Very clean. There’s no trash, no debris. And then you look at the other one and you’ve got about 25 guys. You’ve got brick everywhere. Mortar everywhere. Shovels everywhere. A neater jobsite reduces accidents.
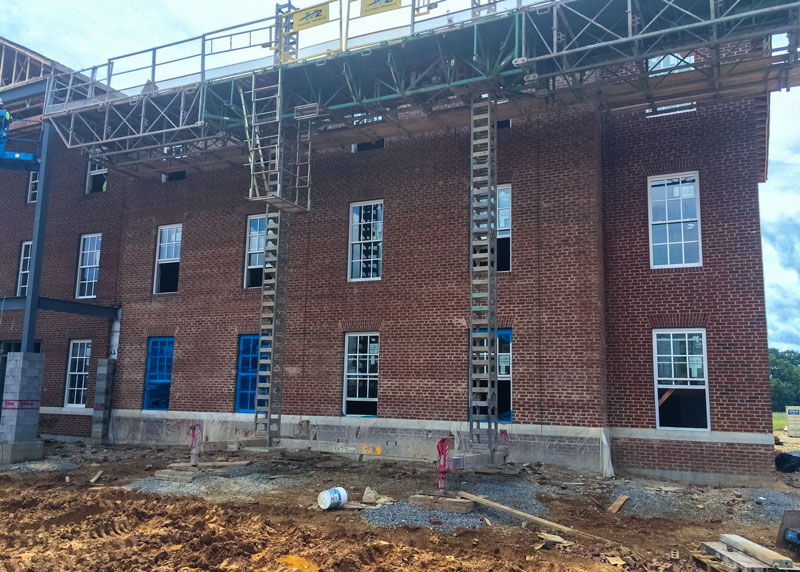
StrXur: Will having automated bricklaying mean brickwork will have to be standardized and lose some of its aesthetic appeal?
Podkaminer: Just the opposite. If you were to design a complex brick wall, it would take just as long as a non-complex wall with SAM, because as the robot’s moving along it knows exactly where to place that next brick. It doesn’t need to stop and think and make sure that it’s in the right spot. It knows. It knows when it needs to do it and the mason’s got a user interface right there and he can see. If anything, technology can make things even more interesting and more appealing. People are used to thinking that the more complex a bricklaying project is, the more it’s going to cost. Once you implement SAM, the cost is the same no matter the complexity of the job.
StrXur: How does somebody get trained on SAM?
Podkaminer: We like to have a three-day offsite training because there is a learning curve: the biggest change with SAM is process. It’s about thinking ahead. Right now, obviously people are thinking ahead but they’re more focused on what’s happening right now. It’s like, “Oh we’re out of mortar. Get more mortar.” But with SAM, if you’re out of mortar, you’ve got to stop the machine, and that takes time. It changes the productivity and efficiency of the guys because it forces them to plan. SAM can lay between 350 to 400 bricks an hour but that’s if it has bricks, it has mortar, and you’re prepared. Then we like to do about a week to two weeks of on-the-job training.
StrXur: How does SAM improve?
Podkaminer: It evolves every day. We’ll be at a job with a new mason and they’ll give us some input and we’ll say, “That’s a great idea. We’ll write it into the code.” We’ve been making it more user-friendly and easier to operate and control. We’re going to continue to drive cycle time down and make more capabilities. SAM’s been able to lay soldier courses now for at least two years, and the process to go from a soldier course to a regular course used to take 15 minutes and now it takes about 30 seconds. That’s mainly because we’ve been learning and we’ve been able to improve on machines.