It takes a lot of technology to artificially recreate what’s found in nature. But, students at Columbia University’s engineering program have recently cracked how to realistically 3D print wood grains and color striations. This is a significant first step toward using 3D technology for carpenters and woodworkers, as well as having applications in working with any material that has complex internal visual qualities.
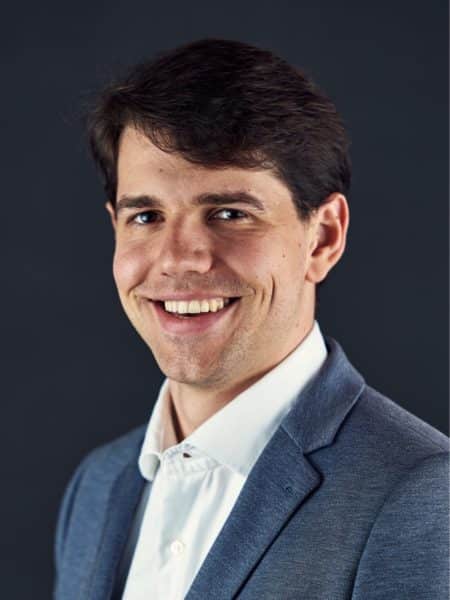
With guidance from faculty advisor Professor Hod Lipson, Ph.D. candidate Joni Mici developed a voxel (the 3D equivalent of a 2D pixel) printing method that’s able to print lifelike 3D wood. If you were to saw through a 4×4 piece of “wood” printed using the voxel method, you’d find color and grain just like that of the real article.
To achieve this feat, the team, which included undergraduate Fabian Stute and master’s degree candidate Lewis Chamberlain in addition to Mici, started by cutting 230 slices of olive wood 27 micrometers thick—about 1/1000th of an inch. Olive wood was chosen for its complex internal color designs and streaks. They fed those samples to a camera-equipped CNC mill, then developed their own codes to program a Stratasys J750 3D printer to print the blocks of “wood.”
Mici’s method is not an immediate disruptor to the existing market for wood. The artificial wood is still plastic—it has the texture of a Lego block and a “mildly sweet smell,” according to Mici, whereas many woods are chosen specifically for their texture or aroma. And, there’s progress to be made in developing other physical qualities, such as weight, hardness and durability. But there’s plenty of research happening now that’s answering those exact questions by printing different materials, including metals, alloys and plastic/metal composites.
For the time being, the price of Mici’s “wood” is significantly higher than the price for regular wood because the resins used are under patent by Stratasys. However, continuing advances in material quality and the normal expiration of patents will create a dynamic market for 3D printing in decades to come.
Consider—the price of a board foot of ebony is approximately $100 due to the rarity and half-inch per year growth rate. It’s also unlikely to fall thanks to increasing demand. At the same time, the price of 3D printing materials and printers is expected to drop as the industry grows and more suppliers get in on the marketplace. Tomorrow’s carpenter hired to install cabinets might not carefully measure, cut, sand, stain and join pieces of ebony—which is famously hard and difficult to work with—but instead simply print pieces out from an essentially limitless design catalog.
Artificial wood and wood composites are currently used primarily for decks, outdoor furniture, or other structures where their durability to the elements gives them the advantage over real wood. Still, there’s no question that real wood is more attractive for designing interior furnishings and fixtures. But if the price of Brazilian walnut flooring—particularly for a large home or office—is out of reach for an owner, the price of printing a 1/8 of an inch veneer of Brazilian walnut that’s indistinguishable from the genuine article offers an extremely attractive option.
There are also advances in the printing of artificial woods for building materials, such as pine. Research engineers are designing 3D printable wood composites that use resin in place of wood’s natural lignin (the natural organic polymer in the cell walls of plants), but follow the same cellular design, essentially replicating the cellular structure of wood with resin instead of biological material, making them resistant to fire, water, and even acid.
There’s a likely future where nobody has to import wood for aesthetic purposes. Any builder could simply download the wood and print it in the exact size desired for purposes of paneling, flooring, doors, shelving and cabinetry or any other design purpose. 3D printed wood could also be attached to cheaper plastics or cured softwood as veneers. While 3D printing won’t affect more specialized uses of wood—such as using ebony in guitars for its sonic qualities or the fragrant oil of sandalwood in perfumes—3D printing could create remarkable changes in the use or value of wood for building and design.
Today, the price of 3D printers, the time of learning how to use them, and the cost of 3D printing materials are still prohibitive enough that many owners, designers and engineers are not making use of the technology. But as research continues, these technologies are poised to become both affordable and ubiquitous. Consider, the first electric drill was patented in 1889, and it wasn’t until 1917 that Black & Decker patented the portable, trigger-switch drill we all recognize. Now, when’s the last time anyone saw a hand drill on a work site?