Concrete is the most ubiquitous building material in the world, with skyrocketing global demand. A critical component of building with concrete is rebar, the steel reinforcement that the concrete is poured around. Typically, however, building rebar cages is difficult and dangerous, because it involves heavy lifting, welding and working in unpredictable outdoor conditions.
That’s the process that New York City-based construction startup Toggle is trying to improve. Toggle serves a 300-mile radius, offering, in its words, “technology-driven rebar fabrication services to urban, energy and infrastructure scale projects.”
Bluebeam talked with CEO and Co-Founder Daniel Blank about how the company got its start, what its technology is like and what sort of projects Toggle is working on.
Toggle was originally founded with an eye toward the construction of industrial scale wind energy. What caused the company to shift toward prefab concrete?
The inspiration for Toggle came from time spent on a construction site for wind energy. The reinforced concrete foundations for wind turbines are enormous structures whose steel reinforcement, rebar, is assembled by hand on site. Our focus at Toggle is to bring technology into the process of producing reinforced concrete structures—critical not only to renewable energy but to all infrastructure as well as urban and other categories of construction. We are still very focused on serving the renewable energy space and have customers in solar and commercial energy storage/batteries already but have broadened our offering to be able to serve all large-scale construction.
You’ve said that you and co-founder Ian Cohen are “working on making construction more like manufacturing, especially for cities and civil infrastructure.” What do you mean by that?
Traditionally, construction is a process done by hand on the construction site where the building or structure is. As we move toward a more urbanized world with greater needs for shared infrastructure systems and dense high-rise structures, we believe that the model for building these types of projects must move in a more manufacturing-centric direction. What that means is more fabrication being done offsite—prefab and then delivered to site for installation or larger-scale assembly. Moving the process offsite reduces the burden of doing the work in increasingly complex and space-constrained environments while also affording the opportunity to develop and implement technology like robotics.
Construction is famously slow to adopt technology, lagging behind only agriculture in the U.S. Do you feel that things are changing?
Yes, absolutely. Ultimately, everyone wants to adopt tools that make jobs safer, reduce errors and increase productivity. That’s what introducing new technology is all about. The challenge with new technology in construction is that it can be risky to try a different approach when you know the current method works. At Toggle, we are also trying to address this risk and shoulder some of the uncertainty for our customers.
What kind of projects are you seeing your product used in?
Right now, our offerings include rebar fabrication and assembly—prefab or “pretied” cages. These are core products to any project that is utilizing poured-in-place reinforced concrete structural elements, which means we can serve a very broad range of customers. We are working on projects that span transportation, energy, marine and urban high rise (residential/commercial).
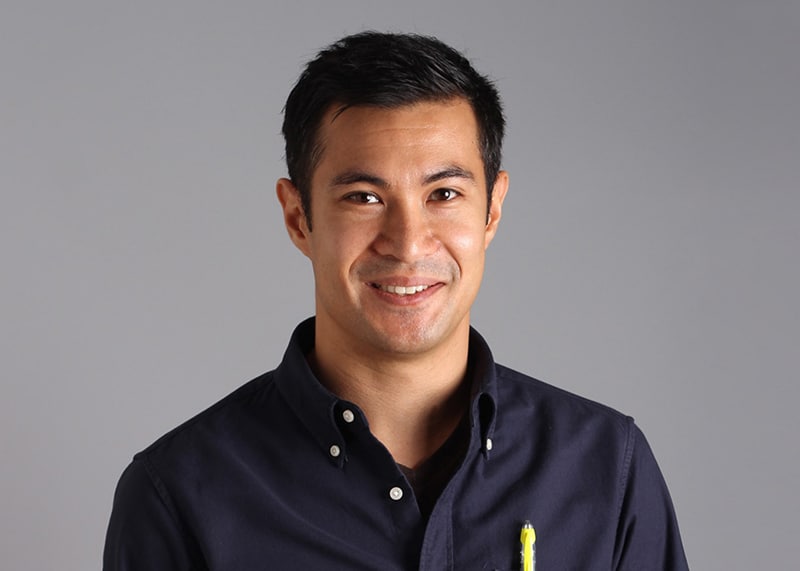
Take me a little bit through the advantages of prefab rebar. When and how is it cost-effective? What are some of the benefits of manufacturing rebar offsite in a controlled factory environment?
Our customers struggle with managing the cost of labor onsite and offsite for fabricating and assembling rebar. If you’re a concrete company, GC or developer with a workforce installing rebar, you know this challenge. What we are doing at Toggle is introducing new tools in a factory environment that allows the same workforce to produce more tonnage every shift ,in a much safer and more controlled environment, ultimately finishing projects faster and allowing for more projects to get done. By allowing industrial robots to do some of the literal heavy lifting, our customers can either get more reinforcement done in the same amount of time or deploy their workforce to other tasks or more parallel projects. Either way, the result is higher productivity—not to mention safety, speed and accuracy.
Can you tell me a bit about the technology involved in the robots building the concrete?
We use industrial robots for what they’re best at—lifting heavy components and specialized tools and placing them into very specific locations over and over again without giving up speed or accuracy. Where our technology comes in is enabling this system to be flexible for use in a construction context. With traditional manufacturing, you’re typically doing the same task and making the same product or set of products repetitively. In construction you need to be able to do nearly infinite variations. Different buildings and different site conditions require different shapes, sizes and variations on those shapes and sizes. So, what our technology does—software for robotic path planning and data processing; hardware for fixturing the assembly; and process for cooperating between people and machines—is enabling rapid switching from one shape and size to the next and one project to the next. No matter how standardized construction may become, it will always require variety.
How do you see Toggle evolving and advancing over the next few years? Are there other construction solutions you’d like to expand into?
Given how important rebar and reinforced concrete is for urban and infrastructure construction, we want to focus on this area and eventually be able to participate globally as a key contributor to the most important shared public systems across categories like transportation, energy, water, housing and others. We definitely see our technology as a platform to enable all different kinds of construction scale assembly, and we plan to both move out of the factory to bring our technology to the site, as well as branch into additional categories like precast.