You may have heard the term digital twin technology without realizing it’s already in your hands.
Google Maps, for instance, is a digital twin that gathers data on traffic, road work, accidents and the speed of your device moving on the road; it then uses those dimensions to present an interactive, real-time map. Also, the engine in your car was tested by a battery of sensors that take in data on performance, creating a digital twin to help the design process.
Technically speaking, a digital twin is a replication of data gathered in real time by sensors operating in many dimensions. For AEC professionals, digital twin technology has such a range of applications that it’s easy to get overwhelmed.
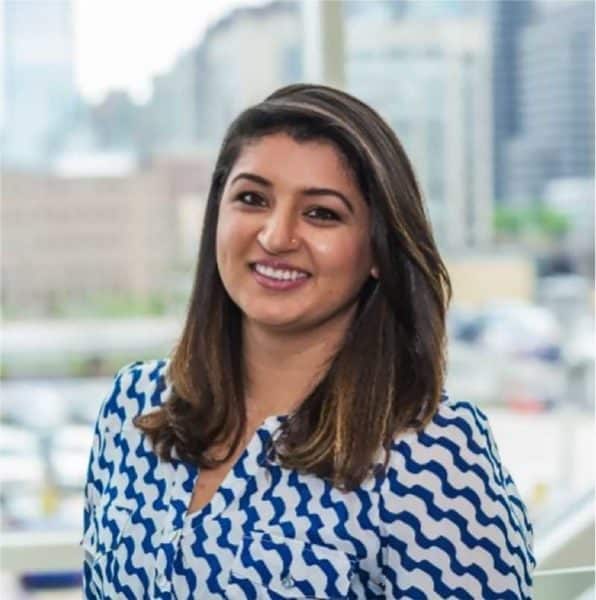
On the small scale, there are smart houses or buildings that regulate lights and air conditioning based on individual preferences. This concept can scale up to entire cities networked to track energy usage, waterworks, public transportation, traffic, population, demographics and even noise or air quality. Singapore, as well as Rennes, France, are currently two cities implementing such capabilities. What’s more, Amaravati, India, is the first city to be built entirely as a digital twin before construction.
Still, there is some confusion over what is and isn’t a digital twin, particularly over the difference between digital twins and Building Information Modeling (BIM). These two technologies can both create lasting value over a property’s lifespan but reach their highest potential when working together.
We spoke to several AEC professionals with experience in digital twin technology and BIM to understand the relationship between these two technologies today and what the future might hold.
Working together
Dan Smolilo, director of process and innovation at The Walsh Group, points out that “BIM and digital twin can run concurrently or divergently … utilizing digital twin can help you operate a facility, but if you throw the concept of BIM in, you can utilize it as your entire location.” Digital twins have long been built into industrial environments such as chemical plants and power stations, where sensors are constantly monitoring performance and safety. Now, there are more sensors drawing data all over, thanks to the emergence of the Internet of Things.
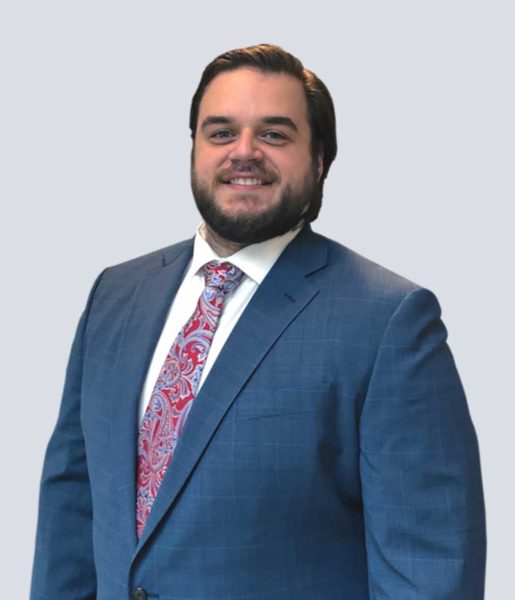
There are, however, challenges to incorporating the technologies cohesively, as described by Amrita Bajwa, an independent BIM coordinator and virtual designer. Bajwa described the roles of various project stakeholders as “silos” that can be difficult to unite. “We use Bluebeam [Revu] because it gets us collaboration, but now we must collaborate on managing the data that’s collected from day one and continues after we’re off the project,” Bajwa said. “There are so many silos, and you have to think about them from a master plan, including the owner, the detailed architect, the contractor, the trades and everyone in between.”
There are also important questions regarding privacy, building regulations and data access. Jeffrey Ouellette, a self-described “recovering architect” who is now an independent technology consultant for the built asset industries, describes four levels of digital twin application.
First, there’s the ability to gather data that you can digitally map. Second, there’s the ability to “leverage that data to operate things on a small scale, such as system automation for lighting, security and elevators,” Ouellette said. Third, you can “connect all of those pieces together and [create] an entire city’s digital twin.” Finally, you can have real-time analytics on the regional level, “but then, the question becomes: What does that digitization look like? What are the communication methods? What does storage look like?”
On the horizon
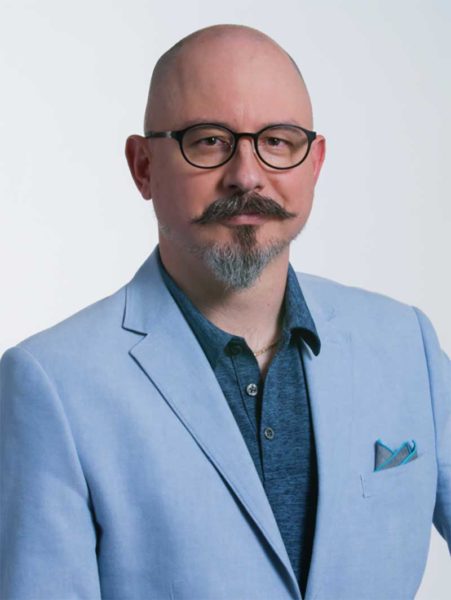
Digital twin technology has advanced slowly into construction and commercial property management—first in the pioneering markets for smart homes as consumer products, but also increasingly on jobsites in the form of GPS chips in heavy equipment or carried by workers for purposes such as tracking performance and location.
Such data is useful for improving performance, as an insurance against theft, and can even be used as proof in a price padding lawsuit. Then there are plenty of interesting tools on the horizon that use digital twin technology, such as WiFi-enabled safety gear that monitors employees’ health while working and augmented reality (AR) headsets so builders can “see” the MEP plans within walls.
Everyone agrees on one thing: a smart building means building smart. If AEC professionals want to fully incorporate digital twin technology to track and predict their property’s performance, start with a solid BIM foundation and incorporate the sensors and data management for a property’s digital twin in the design. People and technology do their best work in collaboration.