Anybody who’s worked in the healthcare construction sector knows: these jobs are tougher than most. Healthcare, and especially hospital construction, is accompanied by some of the strictest inspections. There are oceans of laws and regulations to navigate, and change orders are par for the course, as so often during the time between when, say, a surgery or a lab is designed and when it’s actually built, new innovations change the use cases for that space.
Hospitals are massive projects with teams ranging from designers and architects to medical consultants and community liaisons. It’s an understatement to say they require an incredible amount of coordination and planning.
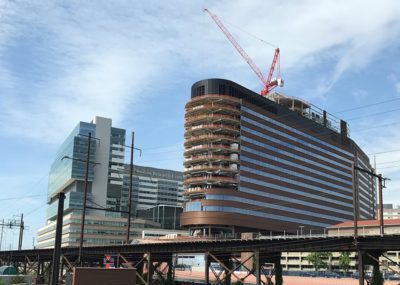
Construction on the Pavilion at the University of Pennsylvania in Philadelphia
So what happens when two organizations known for practicing at the highest level in their respective fields—Penn Medicine for world-class healthcare, Balfour Beatty/L.F. Driscoll Joint Venture (JV) for construction management—team up to build a glimmering new inpatient hospital, called the Pavilion, at the University of Pennsylvania in Philadelphia? The answer is innovation at every level. Even the bathrooms.
Repeatable prefab success
The construction of the Pavilion is complex—it’s an urban site with nearly 1,000 workers. To save space, improve safety and speed up the building schedule, Balfour Beatty wanted to move as many functions as possible into modular processes, offsite. Bathrooms were a great candidate: modular bathrooms are already very much a thing; bathrooms are labor intensive and require the services of a variety of trades; they’re usually, especially in the case of a hotel or hospital, very similar and they’re numerous.
For the Pavilion, the JV team was involved during the conceptual design phase, and helped standardize the bathroom layouts. The result was repeatable, easily manufacturable units. Building the bathrooms themselves helped Balfour Beatty keep labor local, meet exacting specs and produce the pods at a facility nearby. They were able to do the bulk of their QA/QC there, instead of once they arrived at the building site. That means, if any issues were detected, there was no time wasted shipping the unit back to the factory, or having to perform repair work on a crowded site with weather conditions.
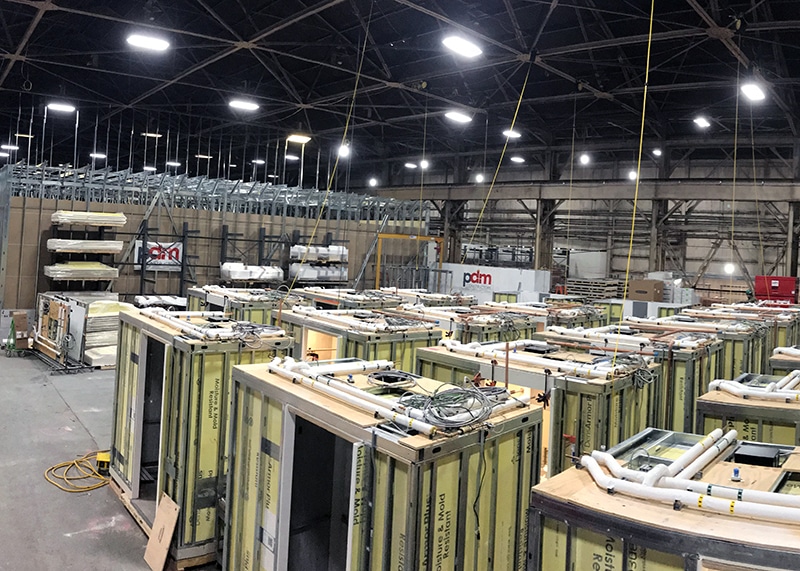
“To support the jobsite, we leased a 60,000-square-foot warehouse,” Andrew Menyo, Balfour Beatty’s project manager overseeing offsite manufacturing for the project, explained. That allowed them to utilize the same labor force as they would have onsite, just in a different location. “One of the big benefits of prefab is shifting that labor offsite where you can reduce site congestion, increase quality, schedule certainty, and cost certainty,” he added.
“Penn Medicine and HDR Architecture were keen on using hygienic, low-maintenance materials. Incorporating solid surface walls and resinous flooring into a bathroom pod would be a challenge if we were buying the pods from an established manufacturer. Keeping the process in house, and through the use of Target Value Design, we exceeded the owner’s expectations and arrived under budget,” Menyo added.
Local team approach
All of this performed in the safe and predictable environment of the warehouse—what Balfour Beatty has termed a Multi Trade Production Facility, or MTPF, which served as a hub for offsite work for key trade partners, and allowed for seamless coordination. This helped streamline costs and processes, and reinforced the build-local ethos of the project team. As much as possible was built with Philadelphia-area labor, even the manufacturing of individual elements, by Balfour Beatty in conjunction with its key trade partner Southland Industries.
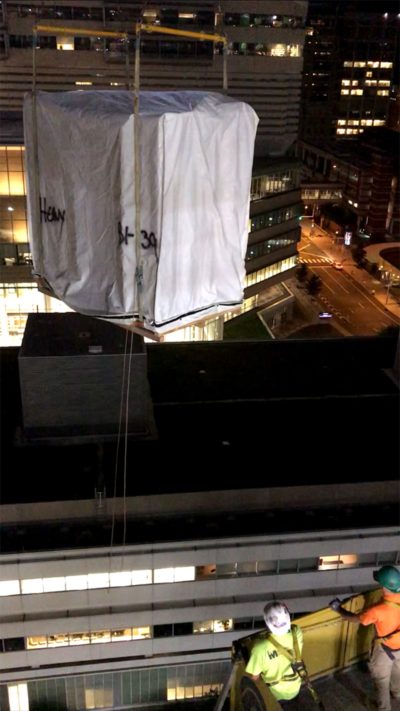
Finished bathroom pod being lifted up by crane to be installed on site
The pace of bathroom construction could be adjusted to track with project construction at large, and once the bathrooms were completed, they were transported just a few miles for installation—and had already been inspected for quality. Balfour Beatty’s flexible and team-oriented approach to the project was true also in their technology adoption—a large part of any job in modern construction.
Amanda Patton, Balfour Beatty’s manager of integrated projects, says that this job in particular was a great example of choosing technology based on what actually works on the ground. “We tested out what we thought would work, but if it wasn’t working for our project, we didn’t keep it,” Patton said. “I think that is a distinction for this job.”
Menyo added, “I’m just blown away at our ability to manage the process so well. The technology’s so pivotal, how digital we really are and how streamlined we need to be to get through the sheer volume of work. I personally have been very impressed.” One key software throughout the project has been Bluebeam Revu, which the team used as a collaboration tool, to communicate during large team huddles as well as with folks out in the field.
Mark Konchar, senior vice president and chief of innovation at Balfour Beatty, has been similarly impressed. “What this team is finding and trying is new, and they’re increasing the speed at which they’re able to do it and everything that flows with it. Getting the trades involved the way this group did, particularly in Philadelphia with the workforce there, is not an insignificant achievement, and seeing them change that dynamic locally, it’s really compelling.”
Now, Konchar plans to bring these benefits and lessons learned to Balfour Beatty teams nationwide. Expect to see innovations that started with the Penn Pavilion project spread far and wide. That’s something we can thank this project team for.