At a gas station in western North Carolina, days after Hurricane Helene tore through the mountains, Stephanie Johnson watched a mother count out quarters to buy food for her kids.
“That’s when I understood that this is really bad,” Johnson said.
Helene had already left Johnson and her family stranded on their property for three days, sawing their way out through downed trees. But the sight of parents scraping for food showed her the storm’s devastation was deeper than wrecked roads and washed-out homes. It was survival.
For Johnson—a former commercial contractor turned real estate agent—that moment launched a mission that has since grown into Rebuilding Hollers, a nonprofit coordinating hundreds of recovery projects. Drawing on her construction background, Johnson built a system that blends supply chain innovation, contractor collaboration and community labor—an approach with lessons for construction professionals far beyond North Carolina’s hollers.
From Chainsaws to Sheetrock: Meeting Material Needs
Johnson leaned on her contracting background to see past the immediate food crisis to the larger task: rebuilding. From fall 2024 to spring 2025, Rebuilding Hollers had distributed at least:
- 400 chainsaws.
- 300 generators.
- 50 water filtration systems.
- Multiple 18-wheeler loads of lumber, sheetrock, siding and other building materials.
Support came from local businesses and national brands alike. Loggers donated lumber, a distributor contributed siding, Ryobi provided tools and a business pooled money to supply sheetrock. An empty storefront became storage space, and Starlink internet helped Johnson coordinate needs quickly on social media.
“It was just amazing how God was sending everything the community needed,” Johnson said.
A Construction-Informed Funding Model
Johnson’s team quickly recognized a familiar challenge for disaster recovery: getting the right materials to the right site at the right time. To solve it, they partnered with Summit Building Supply, a local supplier, to create a gift certificate system tied to each project’s material list.
Here’s how it works:
- Rebuilding Hollers raises funds and directs them into a prepaid escrow at Summit.
- Once a project is approved, the owner receives gift certificates linked to their specific list of materials.
- Families use them at Summit to collect exactly what they need—reducing waste, avoiding mismatched supplies and keeping dollars circulating locally.
For some projects, Rebuilding Hollers also has paid contractors and subcontractors and covered costs at other stores.
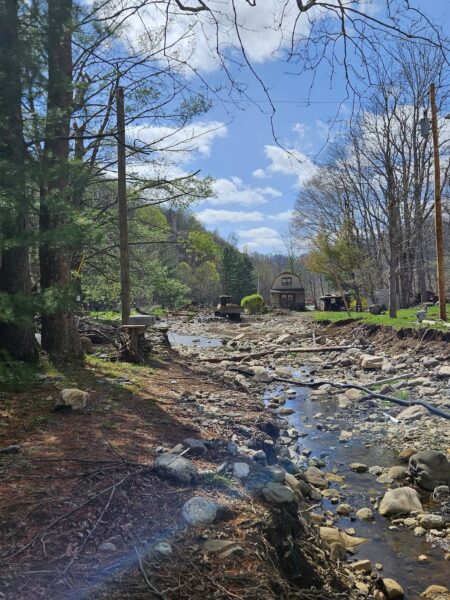
As of spring 2025, the nonprofit has provided more than $284,000 in direct financial support. “It’s totally mind-blowing to me when you really get into what is going on,” Johnson said.
Workforce Partnerships and Skilled Labor
Rebuilding Hollers’ model emphasizes collaboration across the construction ecosystem:
- Local contractors and tradespeople are working alongside families.
- High school carpentry students, through a partnership with the nonprofit, are gaining hands-on training while contributing labor.
- Nonprofits, businesses and individuals have joined in to provide both skilled and volunteer support.
By May 2025, the nonprofit was backing 457 projects—including 51 total losses. Two families had already moved back into fully rebuilt homes with help from the organization.
Rebuilding Communities and Stabilizing Economies
Johnson stresses that rebuilding homes isn’t just about shelter but about keeping the regional economy intact.
“If we don’t rebuild, our entire economy will crash,” Johnson said. “Families will leave, property values will plummet and the community will never recover.”
Tourism is central to the mountain economy, and in May 2025, Rebuilding Hollers hosted a fundraising event that brought tourists into the hollers, both to witness the devastation and support local businesses.
Lessons for the Construction Industry
Rebuilding Hollers’ experience offers several takeaways for professionals across construction, engineering and supply chain sectors:
- Material management systems like project-specific gift certificates can reduce waste and misallocation.
- Local supplier partnerships keep dollars in the community and streamline logistics.
- Blended labor models—combining contractors, student trainees and volunteers—expand capacity in a strained workforce.
- Community-focused rebuilding strengthens not just housing stock but the broader economy.
As Johnson put it: “We’re saying we’re going to stand by you as you rebuild. If you’re brave enough to rebuild, we’re brave enough to get you whatever you need.”