Alex Tanguay is VDC Coordinator at RAD Urban, a vertically integrated design-build firm in Oakland, California. The RAD Urban approach to construction is doubly innovative: designers, engineers and builders all work under one roof to provide modular building solutions to their clients. To date, RAD Urban has completed some of the most celebrated modular projects in the Bay Area, including a 77-unit student housing complex at UC Berkeley, which includes an urban rooftop farm called Garden Village.
StrXur.com recently spoke with Alex Tanguay about modular design, phantom savings, finding the right project and RAD Urban’s plans for nothing less than upending the construction industry.
How long have you been doing modular?
We’ve been at it for close to four years now. Our first modular project was a five-unit apartment building with a car stacker in East Oakland.
Was that your MO from the start?
No, we got our start as a vertically integrated design-build contractor and real estate developer focused on more reliable project delivery through resolution of the misalignment of incentives in traditional contracting structures.
How have you seen a shift toward modular building over the past few years, or do you still see yourselves as being odd folks out?
We see ourselves as more “tip of the spear” than “odd man out.” There is a shift that’s been quietly building up to now. In percentage terms, industrialized construction methods remain a small slice of total construction spending, but we’re seeing exponential growth.
I’ve read about modular building under-delivering on promised cost savings.
This is absolutely true. If you are delivering a traditionally framed six-sided box (four framed walls, a framed floor and a framed ceiling) that happens to be built inside a warehouse, it’s difficult to deliver any real cost savings to the jobsite. Consider that while you may reasonably achieve 30% unit cost savings in the factory due to better production efficiency, once you get to the jobsite, stacking six-sided together means you end up with redundant wall-wall and redundant floor-ceiling assemblies. In practice, your building has 30% more materials than what is actually required, and right there your 30% savings from the factory is gone!
Our approach is to deliver four-sided modules that eliminate structural redundancy and deliver real cost savings. Therefore, a part of the secret sauce lies in managing the challenges of transportation, erection and weather protection of open-sided modules.
What kind of results have you had?
We are growing quickly. We’ve completed $160 million in projects to date including three completed mid-rise modular projects. Our projects have won national recognition for design quality and innovation, while at the same time delivering outstanding returns to our project investors.
Along the way we’ve learned hard lessons which have translated into huge strides in quality control and connection systems.
We have $230 million in projects currently underway and nearly $1 billion in our current pipeline. We’re particularly excited about our upcoming shift from mid-rise to high-rise construction. We have three high-rise projects in our pipeline including what will become the tallest high-rise modular project on the continent and, to our knowledge, the tallest modular building ever built in a high-seismic zone.
What do you attribute your success to?
We’re still a long way from achieving our goal of transforming building construction. But we’ve gotten this far through hard work, discovery, a lack of fear, attention to lessons learned and some really smart people committed to rocking the industry. As a group, we care about the people we build for.
You have a doubly innovative approach. Modular, plus a one-stop shop, with owners, architects, builders, designers and engineers all under one roof. Are you able to separate these two out? In other words, could you be a one-stop shop and do traditional building techniques? Or is there something that really binds the two approaches together?
For us vertical integration is extremely important to what we are doing. Given that our intention is to disrupt the industry using new methods, we require the ability to rapidly communicate across disciplines if for no other reason but to adapt quickly. At this point we aren’t too large and most of us fit in the same room, which is a massive advantage. Communication that could take weeks is broken down in days if not hours or even minutes. And the fact that we are all shoulder to shoulder means ideas can be discussed and analyzed in an open forum, which hopefully gets us to the best solutions.
What types of project are best fits for modular?
Modular works best with scale and repetition. This isn’t to say that small projects don’t work, but they make most sense when assembled out of common modules used across multiple projects. We also have a view that modular works best relative to complex construction in high-cost urban markets. The more expensive the build, the harder an owner should look at industrialized methods as an alternative. Theoretically a high-rise hospital is the ideal modular construction candidate project. In practice, few manufacturers have the technical chops to take on such a project, but this where things are heading.
What do you look for in a project before you take something on?
Location, location, location! Must have the right stuff: transit, food, relevance to workplace, definitely urban, definitely walkable and bikeable. Honestly, we’d rather spend effort on housing people than housing cars.
What have been your most successful projects?
Garden Village, a student housing project for UC Berkeley with an organic rooftop farm, garnered two AIA awards this year, one for design and one for innovation, but to be honest we are still writing history so maybe ask that question in 20 years.
Most challenging?
Every day is a challenge for us but then that’s kind of obvious. Aside from doing something completely different one of our biggest challenges is working with government and citizens to place density. For over 20 years our general population has fought against additional housing in the Bay Area, but slowly folks are realizing that losing two to three hours a day commuting just isn’t high quality of life; it’s both expensive and draining. Let’s face it, for every eight jobs created last year, one housing unit was built and what we are offering is the realistic ability to create housing with minimum impact and at great speed.
We’ve got a lot of work in front of us.
How do you use technology to further your design plans? What are some of the most important technologies for you, and how are you able to innovate leveraging cutting-edge technology of the day?
Technology is vital to our design process and project implementation. We are currently researching technologies from other industries to enhance our module stacking abilities. This is necessary since we are building to tolerances previously unattained in the construction industry. Robotic total stations will play a big role. We are experimenting with VR to evaluate our designs and inform our construction teams.
Bluebeam is also a big part of our process. We are using virtual plan rooms to take advantage of our vertical integration. Design and project teams all have access to the same digital drawing set being used for construction via a dashboard. This ensures everyone is working off the most current information. They all place comments and notes on the drawings. This allows the construction team to get advance notice of changes coming down the pipeline. It also allows the design team to get real-time feedback from the project team. Customizing markup columns and status features allows more information than ever before to be contained in the drawings. With all pertinent information in one place, there is less opportunity for errors due to missed information.
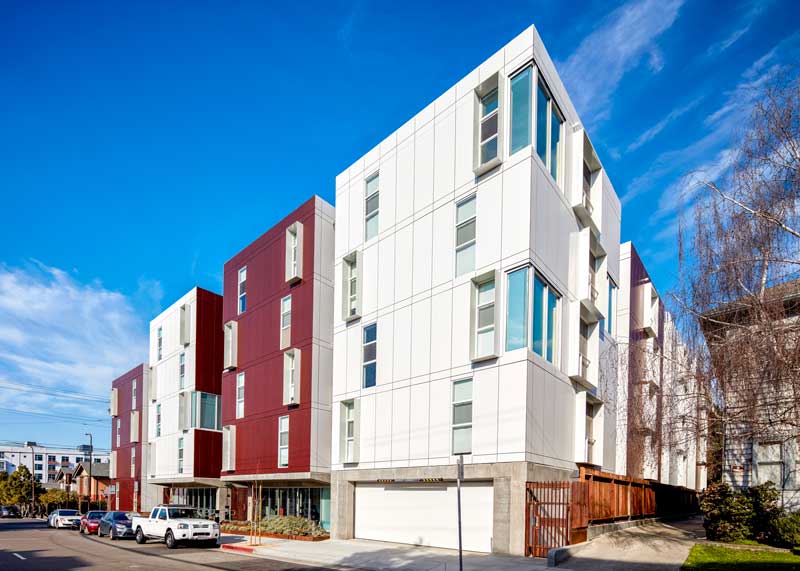
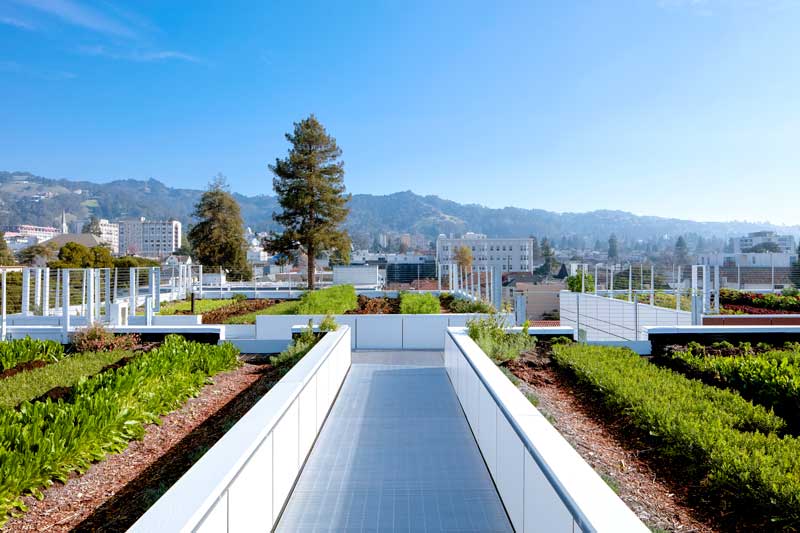