Given the striking glass facade of the new 740,000 square foot California Pacific Medical Center (CPMC) project in San Francisco, it’s easy to wonder how such a design could be realized in a volatile seismic zone like northern California. The hospital’s seven-mile proximity to the notorious San Andreas Fault Line would certainly give a slight pause to the engineers and design team behind this audacious project.
That team would include structural engineering firm Degenkolb, working in conjunction with Modulus Consulting for BIM coordination—and they faced a twofold obstacle. Not only did the building need to withstand actual seismic activity, the 555-bed hospital also needed to satisfy the 2007 California Building Code with OSHPD Amendments for Acute Care Hospitals. Gaining the approval of the Facilities Development Division of OSHPD prior to the build was no small feat. “People are often content with tried-and-true, code-prescribed systems,” explains Jay Love, SEOR for Degenkolb. In order to make the project a success, the teams would have to provide a superior solution to the conventional steel-based Special Moment Resisting Frame (SMRF) technology by supporting a lighter SMRF with an energy-dissipating material, which would be flexible enough to withstand the level of seismic activity necessary to pass code.
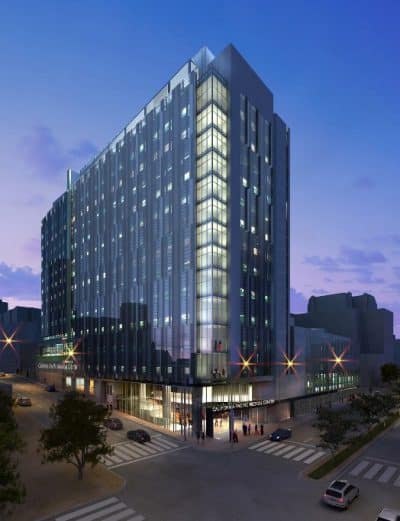
The shift in approach allowed teams to reduce steel by 25% on the project, helping to offset the cost of the damper technology.
The solution came in the form of viscous wall dampers (VWD), or shock-absorbing walls, a technology founded and implemented by Japanese company Sumitomo decades ago. The wall dampers use a non-toxic, odorless transparent fluid called isobutylene between steel vanes of a wall support, and can reduce lateral displacement and superstructure stresses by up to 50%—making them also very cost-effective as they require less steel than typical supports. These VWDs are credited with helping many structures survive the 9.0 Tokoku quake in 2011. Thanks to fabricator and Nevada-based Dynamic Isolation Systems, the concept is finally making its US debut on this project, due to be completed in 2019.
The VWD approach is intriguing: By inserting gel-filled walls to absorb the vibrations of seismic events and heavy winds, teams could design and build without traditional diagonal bracing. Suddenly, the massive exterior glass walls flanking the hospital’s design didn’t seem so impossible. The shift in approach additionally allowed teams to reduce steel by 25% on the project, helping to offset the cost of the wall damper technology.
How do Viscous Wall Dampers Work?
Each VWD is a vertical unit spanning the space between two floors. It is composed of a steel tank filled with viscous fluid connected to the lower floor and a steel inner vane connected to the upper floor that reaches down to rest in the fluid, like a mortar- and gel-filled pestle. When a seismic event or strong motion occurs, the upper vane’s motion is restricted by the fluid, which absorbs vibrations and slows the upper floor’s movement sooner than traditional steel-based damper designs can.
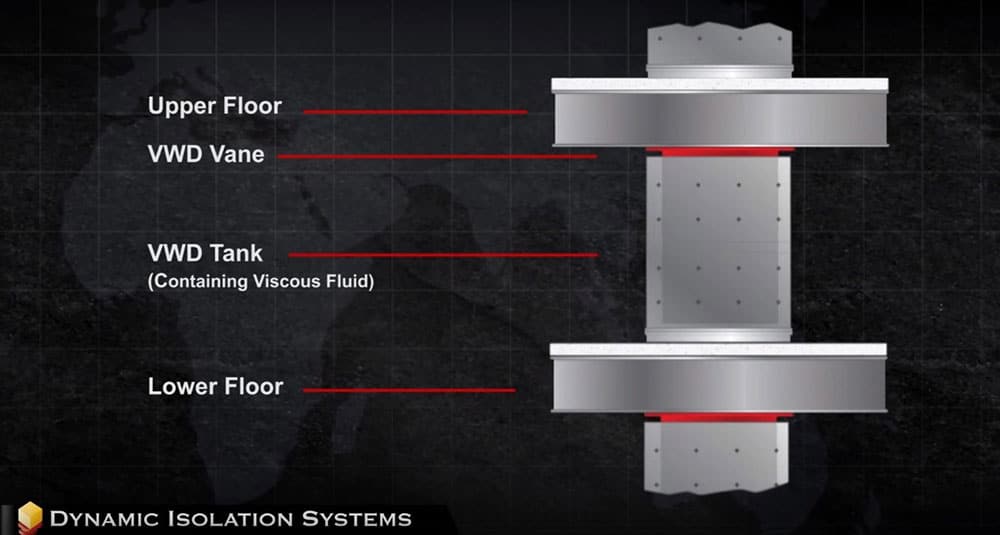
The system of 119 VWDs on the CMPC project is designed to keep the hospital operational in the event of a 7.9 magnitude quake on the infamous San Andreas Fault, notorious for wreaking considerable havoc on Los Angeles during the 1994 6.6-magnitude Northridge quake.
Is VWD Technology Here to Stay?
Despite the challenge of introducing new technology to existing building codes, Degenkolb and Modulus Consulting remain optimistic about VWD success within the states, crediting the technology for being an ideal solution within the complexity of this particular construction site. While project owner Sutter Health has also been drawing some attention to the innovative VWD technology being used on the project, to date no other US building projects have actually committed to using the wall damper systems, so it remains to be seen if the technology will see widespread adoption in US earthquake zones anytime soon.