3D printing is often described as a technology of the future—used to create everything from medical prosthetics to entire homes. But for one Dutch architecture firm, it also provided a surprising window into the past.
Built spoke with Wessel van Beerendonk, director and co-founder of Studio RAP, about the firm’s use of 3D printing technologies to reimagine the classic Dutch Delft tile and how the unique project it created using robotics brings together the best of the old world and the new.
Where tradition meets technology
Beerendonk and his team were tasked with coming up with the design for a building block near Delft central station. “On one hand Delft is the city famous for its Delft Blue porcelain. Nowadays it’s also famous for its innovation,” Beerendonk said. “It has a famous technical university.”
Delft is also famous for a historic city center with many gates, which inspired the design of the PoortMeesters, or gatekeepers, development. Inspired by this design tradition, Beerendonk and his team wanted to create a project that would borrow from the best of Dutch history while bringing a fresh new approach to its design.
“We came up with the idea of New Delft Blue because we were already pioneering at our architecture firm with 3D printing ceramics and this was the ideal application for it,” Beerendonk said. “It looks in the past, but it also looks to the future.”
Beerendonk and his team referenced the traditions of classic Delft china as they dreamed up their New Delft Blue designs. “When you look at Delft Blue porcelain plates, you see the recurring theme of the decorative frame and the idyllic scene, so you see a lot of flowers and leaves, patterns, etc.,” he said. “When you’re in front of the gate and you look into the courtyard, you see the idyllic scene, and we use the gate itself as the decorative frame.”

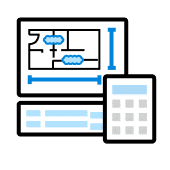
Bluebeam Resource Hub
Browse case studies, watch webinars, and see what’s new with Bluebeam.The frame design of the gateway tile updated the repeating designs used in traditional Delft tile with an algorithmically driven spin. “We programmed in our computers the growth of leaf patterns that guide you as a user from the public space to the semi-public space, the courtyard,” Beerendonk said. “That resulted in roughly 3,000 unique 3D printed tiles. They’re all unique.”
The team designed two gates that would move the visitor from the public spaces of the street to the semi-public spaces of the courtyard. “Every time that you walk through the gate, you see something else; you see a different leaf and that gives it, in our opinion, a certain timelessness and you never get bored,” Beerendonk said.
An in-house robot workshop
This type of technology forward thinking is nothing new for the Studio RAP team.
“At our robot workshop, we are not a traditional architecture firm. We are architects, but we also have our own robot workshop where we develop technology that we apply in our architectural designs,” Beerendonk said.
He said the blending of design and technological innovation this project required is fairly typical for the team. “It’s actually in the DNA of our company,” he said. “My business partner and I started the studio, when we saw this gigantic leap in technology and in innovation in other industries. We were actually pioneering algorithmic design and robotics at the university, and we saw a unique opportunity to actually challenge the status quo of that time. At the very beginning of our studio, we were already developing technology.”
Beerendonk believes that this twin focus helps Studio RAP stand out. “We tried to differentiate ourselves from other architects to get assignments in, because it’s quite competitive in the Netherlands; we have a lot of good architects here,” he said. “We thought, ‘OK, we see this unique opportunity of giving more services to our clients.’ Not only design, but also to deliver technology or deliver something very special.”
Studio RAP’s gambit paid off. “We started pioneering in the field of robotics, programming, algorithmic design, and it actually grew quite fast,” Beerendonk said. “Now we are with eight people and three robots.”
On-demand innovation
Beerendonk said the scale of this project allowed the team to take a novel approach to the idea of 3D printing as a tool for construction.
“I think that it was interesting to develop the technology with that scale in our minds, because you see a lot of printing technology nowadays, but it’s always based on a very small scale,” he said. “The industry is becoming quite mature at the moment, but in the construction industry, it’s not that mature yet and I think it also has to do with the difference in scale. You have to really print so much volume.”
The need for volume also meant a need for speed. “When you take that as a starting point, you also develop your hardware in a different way, because you need to print fast. One tile is printed in 12 minutes, but then still it takes almost half a year to print the gate because it’s 335 square meters.”
To get to this rapid rate of printing, Beerendonk said the team had to innovate every step of the process. “We developed a new material ourselves, and we developed a technology ourselves,” he said. That’s actually how it started, and then when we had the design, we knew what to make exactly.”
Still, Beerendonk said the team had a number of issues to resolve that popped up along the way. “It’s 3D, all these tiles are engineered, so how do we get proper glaze on it? But that was also quite a ride to get the right colors. That was also a big challenge because all tiles are unique, so how do you do that? What happens if one breaks?” Even though it took some doing, Beerendonk said the response to the project has made all that effort worthwhile. “People see it everywhere around the world, and they really appreciate it. They see the craftsmanship and the innovation and the uniqueness in it.”